Thesis
In 2022, iron ore was the most mined metal in the world, representing 93% of all metals extracted. Iron is the raw material that is essential for steel production, which traditionally relies on coal-heavy processes. In 2023, coal comprised 75% of the global fuel mix used in steelmaking. For every ton of steel produced, there are 1.9 tons of carbon dioxide emitted. As of 2023, 8% of global greenhouse emissions were attributed to the steel industry.
However, there is a growing movement to lower carbon emissions from steel production, with some steel manufacturers aiming to achieve net-zero emissions steel by 2030. In April 2021, US Steel, the second largest steel enterprise in the US, announced that it aimed to achieve net zero greenhouse gas emissions by 2050. Subsequently, in November 2023, the largest US steel manufacturer, Nucor set its net zero commitment by 2050.
Boston Metal is developing a cleaner process to create steel through its Molten Oxide Electrolysis (MOE) technology, which uses renewable electricity to produce steel without emitting carbon dioxide. This technology eliminates the need for traditional, carbon-intensive processes, significantly reducing the environmental footprint of steel production. By offering a cost-effective and zero-emission solution, Boston Metal addresses regulatory pressures and market demand for the production of green steel, which has been defined as steel manufactured without the use of fossil fuels.
Founding Story
Boston Metal was founded in 2012 by Donald Sadoway (former CEO), Antoine Allanore, and Dr. Jim Yurko (former President). The core MOE technology was developed at MIT, where the team met in Sadoway’s laboratory with the help of NASA and the American Iron and Steel Institute.
In the 1980s, Sadoway began researching the electrochemical production process for aluminum. The research objective was to identify a replacement for the anode used in that process. While working on this project, Sadoway began applying a similar electrochemical process to make iron. Sadoway and his students worked on a process called molten oxide electrolysis and proved that this method could produce metals, including steel, at scale.
In 2012, Sadoway and Allanore, former MIT postdoctoral associates, discovered an iron-chromium alloy that could be used as a cheap anode material. This enabled the team to build a commercially viable process that produced oxygen as a byproduct rather than carbon dioxide. The pair then partnered with Yurko, a former student of Sadoway, to launch Boston Metal.
By 2014, the company commissioned its first semi-industrial MOE cell. Tadeu Carneiro (CEO) stepped in to replace Sadoway as CEO in 2017 after serving as CEO at CBMM, the world’s largest producer of niobium. Guillaume Lambotte (Chief Scientist), an early employee at Boston Metal, reflected on the company’s origin in a 2013 paper:
“We spun out of research that was patented at MIT and licensed from MIT’s Technology Licensing Office…That’s when it went from the lab, with a coffee cup-sized experiment to prove the fundamentals and produce a few grams, to a company that can produce hundreds of kilograms, and soon, tons of metal”.
Product
Boston Metal is focused on commercializing MOE, which allows for the production of steel using electricity instead of fossil fuels like coal. As the company describes it, “MOE provides the metals industry with a scalable, cost-competitive and modular technology for the production of green steel from all iron ore grades.” The ubiquity of steel in everything from hardware to the built environment points to the scale of the undertaking needed to decarbonize steel production. As Vaclav Smil, the author of Still the Iron Age, put it in 2016:
“Steel is truly a ubiquitous material: there is no industrial enterprise that would not, directly or indirectly, rely on it. There is no modern construction activity that can proceed without it... There is no commercial or household activity that would not, or ultimately, owe its existence to it.”
Molten Oxide Electrolysis
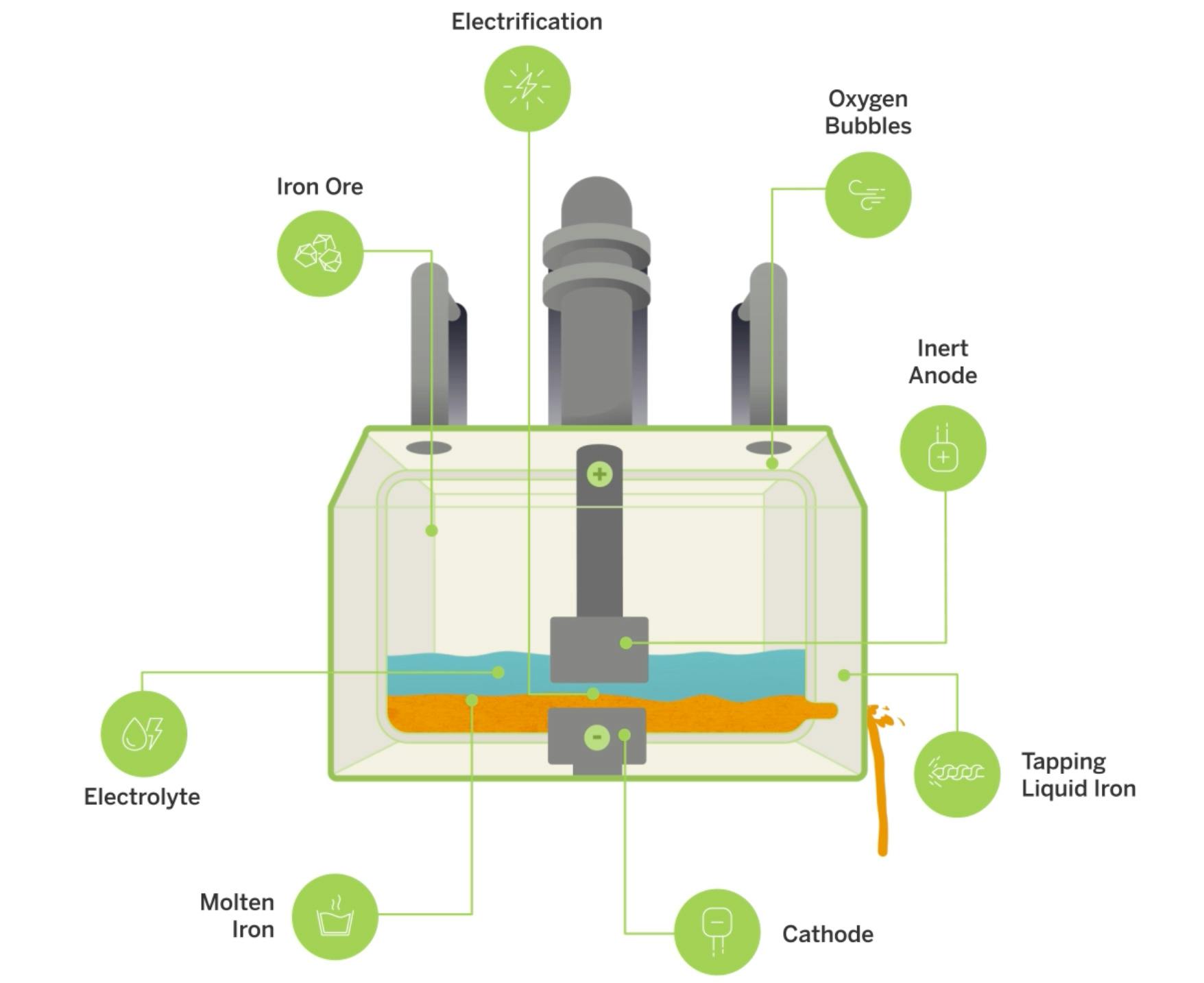
Source: MIT News
Boston Metal’s MOE process runs in modular MOE cells, which are roughly the size of a school bus. Iron ore rock is introduced into the cell, which houses the cathode (negative terminal) and an anode (positive terminal) submerged in a liquid electrolyte. The anode is inert, meaning it does not dissolve in the electrolyte or participate in the reaction beyond serving as the positive terminal.
When electricity flows between the anode and cathode and the cell reaches approximately 1.6K degrees Celsius, the iron oxide bonds in the ore are broken, resulting in the production of pure liquid metal at the bottom, which can be extracted. The reaction produces oxygen as a byproduct, and the process does not require water, hazardous chemicals, or precious metal catalysts. Each cell’s production is a function of the size of its current. With 600K amps, each cell could produce up to 10 tons of metal daily.
Steelmaking Processes
Boston Metal describes its MOE process as a simpler, more energy-efficient, and lower environmental impact method of production than traditional steelmaking methods. It enables mining companies to generate new revenue by using MOE to extract valuable metals from low-concentration materials that are considered waste. Unlike many green steel solutions that rely on scarce high-grade iron ores, MOE technology can produce high-quality liquid steel from the more abundant medium and low-grade iron ores.
The process of refining iron ore into steel begins with mining iron ore (Fe₂O₃), which is an impure iron oxide. Iron is primarily found in Australia, Brazil, India, China, Russia, Europe, and South Africa. The ore is then heated and reacts with a reductant such as carbon, hydrogen, or methane. Limestone is added and reacts with silicates in the iron ore and forms slag, which is removed. Pig iron is the substance that remains, which consists of 90% iron and 10% carbon.
This pig iron is then placed into a basic oxygen furnace (BOF) where high temperatures and oxygen remove the carbon, producing carbon dioxide. The viscous hot metal is poured into molds to form ingots and cool into a final product.
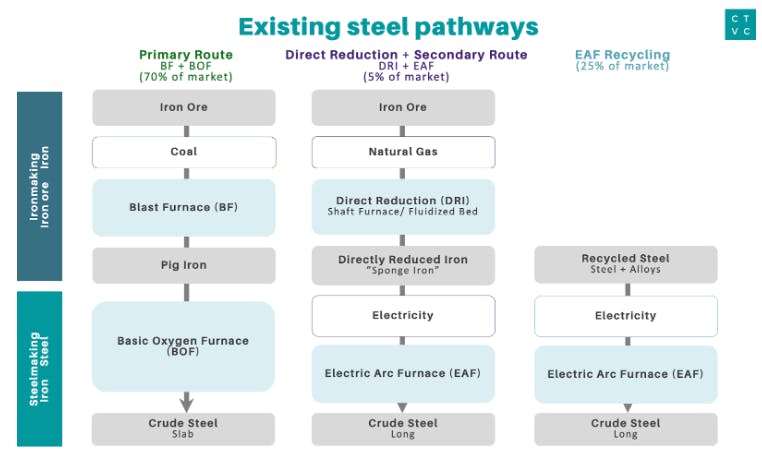
Source: CTVC
There are three main methods of steelmaking. As of 2022, the primary route made up 70% of the market share with direct reduction consisting of 5%, and EAF recycling consisting of 25%.
Primary Route: Also known as integrated steelmaking, this process starts with converting iron ore into pig iron in a blast furnace using “coked” coal. The pig iron, containing about 4% carbon, is then processed in a BOF where oxygen is blown over the molten metal, reducing the carbon content to about 1% and forming carbon dioxide. This method processes raw materials into steel.
Directly Reduced Iron: Directly reduced iron involves reducing iron ore using natural gas or hydrogen. The reduced iron is then melted in an electric arc furnace (EAF), with minimal coal added to provide the necessary carbon for steel production. This method is more flexible and can be more environmentally friendly due to the use of cleaner reducing agents. Boston Metal is utilizing this method in its MOE process. The company runs electricity through a solution containing iron ore at 1.6K degrees Celsius to produce pure liquid metal.
Secondary Route: This route focuses on recycling scrap metal. Scrap, often containing alloys, is melted using electrodes in an EAF to produce crude steel. This process is energy-efficient and environmentally beneficial but typically results in lower-grade steel due to the varied composition of the recycled metals.
Inert Anodes
Boston Metal's inert anode is a key component in their MOE technology, enabling the production of steel without carbon emissions. Unlike traditional carbon-based anodes that emit carbon dioxide during steelmaking, these inert anodes do not participate in the chemical reaction, thereby eliminating carbon dioxide emissions. Composed of metallic materials capable of withstanding high temperatures and corrosive environments, the inert anodes facilitate the electrolysis of iron ore at approximately 1.6K degrees celsius, resulting in the production of pure liquid iron and oxygen as a byproduct. This innovation allows for continuous steel production without the need for frequent anode replacements, enhancing operational efficiency and sustainability.
Market
Customer
Boston Metal's primary customers are steel manufacturers looking to reduce their carbon footprint and adopt more sustainable production methods. The largest steel producers are located in China followed by India, Japan, and the US. China Baowu Steel Group, the world's largest steelmaker, produced 130.8 million tons, or 7% of the world’s steel, in 2023. Nucor, the largest US steelmaker was responsible for 21.2 million tons of steel production or 1% of global steel production placing it as the 15th largest steel producer in 2023. These could represent potential customers for Boston Metal’s technology.
Boston Metal also requires markets where renewable energy makes a large share of energy penetration. Its MOE process requires the electricity to be clean and in order to make 1 million tons of steel per year, a manufacturer would need 500MW of electricity. As of 2023, China’s renewable energy penetration is 31% followed by Japan at 24% and the US at 23%. As the cost of renewable energy has plummeted since 2013, clean electricity will be more widely available and green steel could be cost-competitive relative to incumbent steelmaking methods. The DRI-EAF method of steelmaking only constitutes 5% of the steelmaking market versus 70% of the market share from the incumbent blast furnace method. The DRI method is cost-competitive at $40/MWh.
Market Size
Boston Metal operates within the global steel market, which was valued at $1 trillion in 2023 and is expected to grow at a 4% CAGR to reach $1.7 trillion by 2031. In 2023, Asia dominated steel production, accounting for 74% of the global output, which translated to 1.4 billion tons. Within Asia, China led steel production, contributing to 54% of the world's steel, followed by India at 7%, and Japan at 5%. North America, by comparison, only produced 6%. Overall, global steel production reached 1.8 billion tons in 2023.
Competition
Stegra: Founded in 2020, Stegra, formerly known as H2 Green Steel, focuses on the production of green steel using hydrogen instead of coal. The company aims to revolutionize the steel industry by significantly reducing carbon emissions associated with steel production. Stegra's process involves using green hydrogen, which is produced through electrolysis powered by renewable energy sources, to replace the traditional carbon-intensive methods. The company's goal is to create a more sustainable steel production process, reducing carbon dioxide emissions by up to 95% compared to conventional methods. CEO Henrik Henriksson has said that customers such as BMW and Porsche have been willing to pay a roughly 25% premium for green steel over conventional steel.
Stegra and Boston Metal both aim to decarbonize steel production, though they use different methods. Stegra utilizes green hydrogen to reduce iron ore into steel with minimal emissions, while Boston Metal employs MOE, which uses electricity to produce steel without direct carbon dioxide emissions. In January 2024, H2 Green Steel raised €4.2 billion in debt financing, €250 million in grant funding from the European Union's Innovation Fund, and €300 million in equity from investors such as Microsoft Climate Fund, Mubea, and Siemens. The company is building a plant in Boden, Sweden, which will use green hydrogen from 2025 onwards.
Electra: Electra, founded in 2020, produces green steel through electrochemical processes. The company's approach involves using electrolysis to produce iron from low-grade ores and mining waste, which is then converted into high-quality steel. Electra has attracted substantial investment to develop its first commercial-scale plant, projected to begin operations in 2025. The difference in Electra’s product is that it dissolves iron ore in an acid-based solution and doesn’t require high temperatures to produce steel.
Electra and Boston Metal are developing technologies to decarbonize steelmaking but with different approaches. Electra uses low-temperature iron ore electrolysis powered by renewable electricity to produce zero-emission iron, which can integrate with existing steel infrastructure. Boston Metal employs high-temperature MOE to directly produce liquid steel without emissions, aiming to replace traditional steelmaking entirely. Electra focuses on compatibility and smaller-scale applications, while Boston Metal targets a comprehensive transformation of the industry.
In October 2022, Electra secured $85 million in a funding round led by Breakthrough Energy Ventures, Amazon, BHP Ventures, Capricorn Investment Group, Lowercarbon Capital, and Valor Equity Partners. Electra’s total funding is $113.5 million as of December 2024.
Business Model
Boston Metal is not a traditional steel manufacturing company. Instead, it operates as a technology provider for steel manufacturers. Rather than producing steel itself, Boston Metal licenses its MOE technology and provides the necessary anode materials for executing the process. This one-step process is designed to be cost-competitive with traditional steel-making processes at an electricity cost of $40/MWh.
In addition to licensing, Boston Metal manufactures and markets its metallic inert anodes, a critical component of the MOE cells. This strategy allows Boston Metal to scale its technology by partnering with established steel manufacturers and leveraging their infrastructure and expertise.
Boston Metal has outlined its path toward commercializing its MOE technology. By 2026, the company aims to begin licensing its first commercial-scale application, coinciding with the construction of its inaugural industrial facility.
Traction
Boston Metal launched its first commercial deployment for the MOE technology in March 2024 in Brazil. This plant, managed by its subsidiary Boston Metal do Brasil, employs 80 local workers and operates entirely on renewable energy as of May 2024.
In 2024, the company developed a prototype MOE reactor at its headquarters in Woburn, Massachusetts, to produce green steel. Additionally, Boston Metal was been selected by the US Department of Energy to establish a chromium metal manufacturing facility in Weirton, West Virginia in March 2024. This plant will domestically produce materials critical for the aerospace, chemical processing, and nuclear industries.
In April 2020, Boston Metal partnered with CBMM, a global leader in niobium products, to trial its MOE technology for the production of niobium materials. This collaboration aimed to enhance the sustainability and efficiency of niobium production, further demonstrating Boston Metal's ability to adapt its MOE platform for applications beyond steel. The partnership highlights the scalability and versatility of Boston Metal's technology in industrial decarbonization.
Valuation
Boston Metal secured $20 million in a Series C2 funding round in January 2024 and a $262 million Series C in September 2023, bringing the total amount raised in its Series C round to $282 million at an undisclosed valuation. As of December 2024, Boston Metal’s total funding is $352.7 million. New investors in the Series C round included Aramco Ventures, M&G Investments, Goehring & Rozencwajg, and Baillie Gifford. Existing investors that also joined the round included Breakthrough Energy Ventures, Microsoft’s Climate Innovation Fund, BHP Ventures, and Prelude Ventures. Although the company’s valuation is unknown as of December 2024, Carneiro stated that “despite the challenging market conditions, Boston Metal’s valuation continues to increase” in January 2024.
Key Opportunities
Partnerships with Mining Companies
By collaborating with mining companies, Boston Metal can leverage its MOE technology to extract high-value metals from mining waste, transforming waste into valuable resources. This approach not only boosts the profitability of mining operations but also aligns with circular economy principles, reinforcing Boston Metal's commitment to sustainability. Such partnerships demonstrate the practical and economic viability of turning waste into assets, creating new opportunities for resource efficiency.
Expansion into Emerging Markets
Emerging markets such as India and Brazil, with their expanding infrastructure demands, present growth opportunities for Boston Metal. Establishing strategic partnerships and collaborations in these regions allows the company to tap into the demand for sustainable steel solutions. This expansion not only supports global decarbonization efforts but also opens up new revenue streams, enhancing Boston Metal’s market presence and influence in the global steel industry.
Applications of MOE in Various Metallurgical Processes
There are multiple applications of the MOE process that can be applied to a variety of feedstocks that contain oxides. The MOE technology can be adapted for the production of chromium, a critical material for the aerospace, chemical processing, and nuclear industries, and the refining of nickel and cobalt, essential metals for battery production and other high-tech applications. By applying the MOE process, Boston Metal can produce high-purity chromium metal domestically, enhancing supply chain security and reducing reliance on imported materials.
Key Risks
Supply Chain Dependencies
Boston Metal's operations rely on the availability and cost of key inputs such as iron ore and renewable electricity, which are critical to its MOE technology. Disruptions in the supply chain or price volatility could affect production costs and schedules. The company’s ability to compete with traditional steelmaking processes depends on access to inexpensive and reliable renewable energy, essential for maintaining operational efficiency and achieving cost parity.
Intellectual Property
Boston Metal's growth depends on its innovation, robust research and development, and proprietary patents related to MOE. The company faces risks related to intellectual property, including potential infringement or challenges in defending its patents against competitors. As competition in the clean steel market intensifies, new entrants may develop patents on alternative processes or technologies that could restrict Boston Metal's ability to operate freely or adapt its technology. Protecting and defending its intellectual property will be essential for sustaining innovation and maintaining a competitive edge.
Renewable Energy Development
Boston Metal's business model is contingent on the availability of cheap and reliable renewable energy. The production of green steel using MOE technology requires significant amounts of renewable electricity. Any delays in renewable energy infrastructure development or increases in energy prices could adversely affect the cost structure and scalability of Boston Metal’s operations. The viability of producing green hydrogen, a key component in the MOE process, depends on the cost-effectiveness and reliability of renewable energy sources like wind and solar power.
Summary
Boston Metal could transform the steel industry with its MOE technology, which produces steel using renewable electricity without emitting carbon dioxide. This process eliminates the need for fossil fuels, significantly reducing the carbon footprint of steel production. The company aims to commercialize its MOE technology by 2026, offering a scalable, cost-effective solution that can be licensed globally to accelerate the adoption of sustainable steelmaking methods. As steel manufacturers are making net-zero pledges across the world, Boston Metal hopes to provide a sustainable solution that is cost-competitive with traditional processes and move the building blocks of the built environment forward.