Thesis
In 1909, Fritz Haber developed the process to synthesize ammonia from atmospheric nitrogen - a breakthrough that unlocked industrial-scale fertilizer production and transformed global agriculture. Over the next century, the Haber-Bosch process fed billions, enabling Earth’s population to grow from 1.6 billion to more than 7 billion. But the same innovation that enabled abundance also entrenched the use of fossil fuels as the foundation of modern industry.
The global chemical industry is responsible for converting oil, gas, and coal into the materials behind nearly every manufactured product: plastics, fuels, pharmaceuticals, coatings, and more. In the US, it supported over 25% of the total GDP and was a $600 billion market in 2023, with 96% of goods produced in the US containing chemical products in their manufacturing process. Globally, this is a $6 trillion industry and one of the largest sources of industrial emissions, consuming 10% of generated energy and emitting more CO₂ than all transportation combined. Despite decades of sustainability pledges, the underlying infrastructure has remained carbon-intensive, centralized, and hard to replace.
Simultaneously, a new infrastructure race has begun. The growth of AI systems is pushing power, cooling, and materials demand to unprecedented levels. By 2028, data centers could consume up to 12% of electricity in the US. But as seen in past industrial shifts, constraint drives innovation. Just as the semiconductor industry broke through its power wall with chip designs, the next wave of industrial systems will require rethinking physical inputs from first principles - including the chemical supply chain beneath it all.
Solugen is building a new foundation. By combining enzyme engineering, metal catalysis, and AI, the company has developed a modular manufacturing platform that produces high-performance chemicals from renewable feedstocks, at an industrial scale, and with carbon-negative economics. If successful, Solugen could become the first decentralized, fossil-free alternative to legacy chemical infrastructure — positioning it as a critical enabler of both the energy and AI transitions ahead.
Founding Story
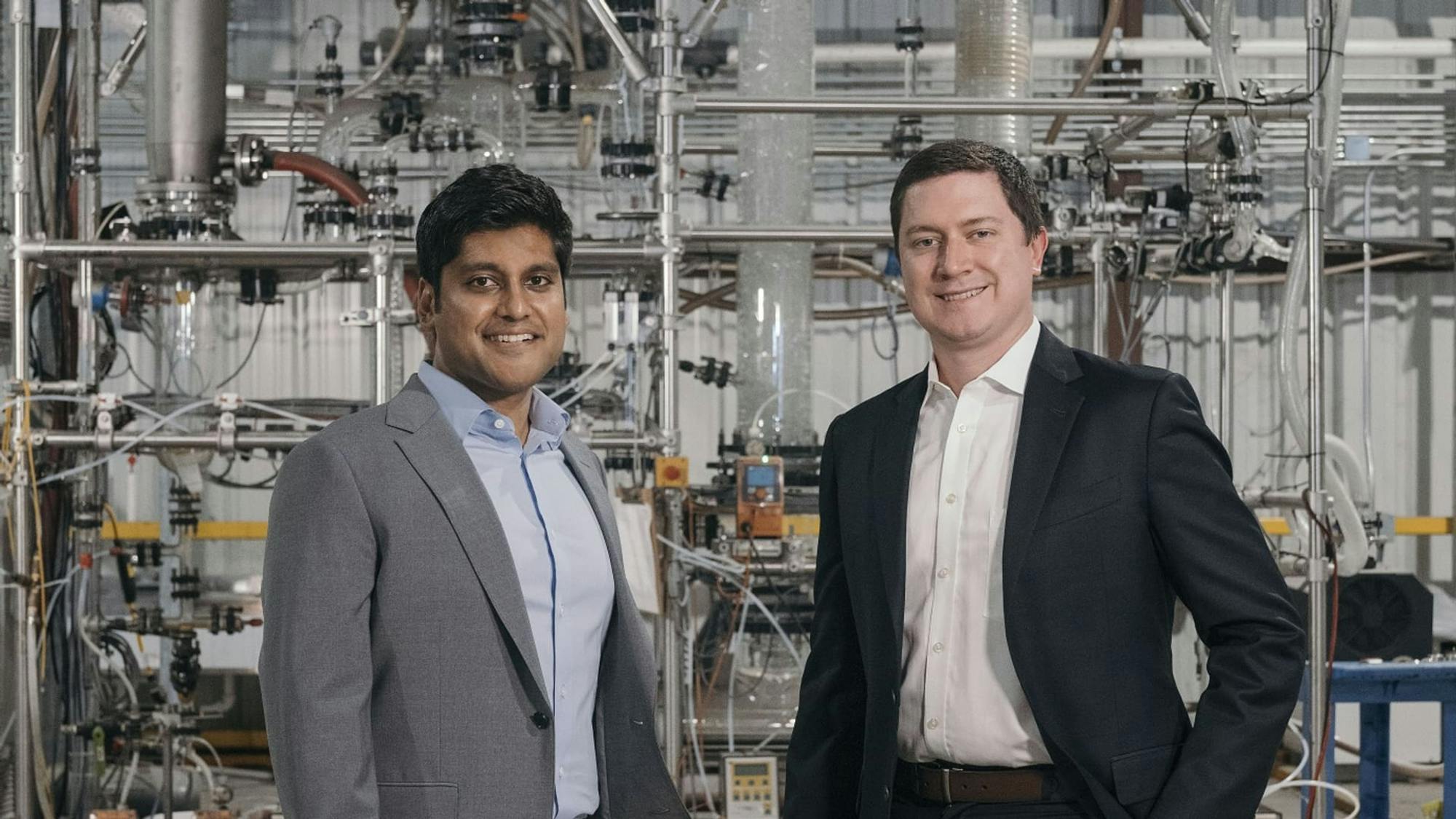
Source: CNBC
Solugen was founded in 2016 by Gaurab Chakrabarti (CEO) and Sean Hunt (CTO). The company originated from their shared interest in developing a low-emission, cost-efficient process to produce hydrogen peroxide using enzymes and metal catalysts.
Chakrabarti’s background is in computational biology and oncology. While pursuing a Ph.D. and M.D. from UT Southwestern (Dallas) from 2010 to 2017, he worked in a cancer biology lab to uncover why pancreatic cancer cells produce excessive hydrogen peroxide, a reactive oxygen species, causing DNA damage. While developing a drug to prevent this damage, Chakrabarti discovered the enzyme responsible for the production of hydrogen peroxide. His research proved that cancer cells produce profound quantities of commercially viable chemicals, and he found a way to replicate the process outside the body, by converting sugar to hydrogen peroxide through an enzyme.
Hunt’s background is in chemical engineering. He earned his PhD from MIT in 2016 and began his work with metal catalysts during an internship at the Philadelphia Naval Shipyard. His research at MIT focused on scaling the production of hydrogen peroxide using metal-based synthesis methods. He was particularly interested in replacing traditional petrochemical inputs with lower-emission alternatives.
The two met in Texas during a visit by Hunt to see his then-girlfriend, now wife, who was Chakrabarti’s medical school lab partner. At a poker game in 2015, they began discussing their respective research. Initially skeptical, Hunt dismissed the biological process. However, after continued conversations and a petrochemical plant explosion in Dallas, both saw the potential in combining enzymatic and catalytic methods to produce hydrogen peroxide more safely.
In early 2016, the pair entered the MIT $100K Entrepreneurship Competition with a business plan based on this hybrid chemo-enzymatic approach. They were selected as finalists and received a $10K grant. Potential customers were in attendance at the competition and told the co-founders that they would buy hydrogen peroxide from them, so Hunt rushed to Home Depot to buy parts for their first reactor.
The $7K PVC pipe reactor they assembled in a small lab behind the Dallas Love Field Airport cost $150/month to maintain and was capable of producing five gallons of hydrogen peroxide per day. Initially, the pair loaded buckets of the cleaning solution in the back of Hunt’s Subaru and drove to float spas and other customers they found by contacting these businesses on Facebook, eventually capturing 80% of the US float spa market by 2018.
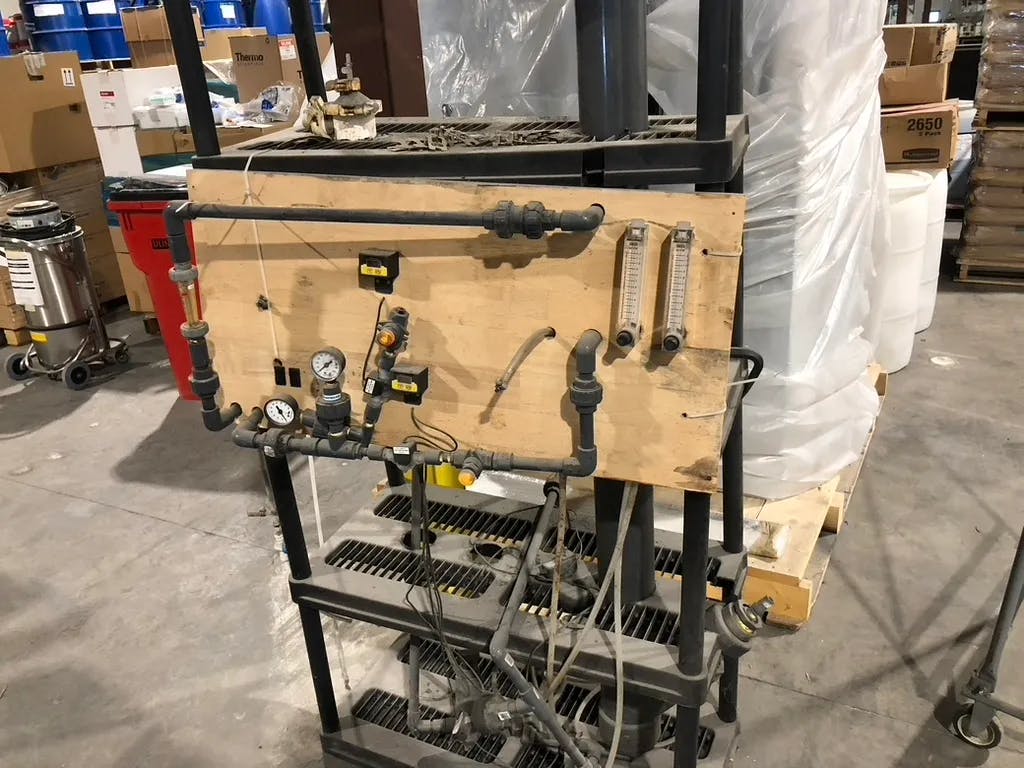
Source: Century of Bio
In 2017, Solugen joined Y Combinator’s winter batch. In the same year, Solugen signed a deal with wet-wipe manufacturer Diamond Wipes and launched a new brand called Ode to Clean. Diamond Wipes manufactured the wipes, while Solugen provided hydrogen peroxide and marketing. After a few weeks of producing Ode to Clean at $4-5 per pack, Solugen was scheduled to generate more than $4 million from the partnership in its first year.
Not only was hydrogen peroxide the main ingredient in the antiseptic, but its production burned a lot of fossil fuel — it was estimated that one could fly to the moon and back 18K times with the amount of petroleum used to make cleaning wipes every year in the US alone. Ode to Clean was acquired by Diamond Wipes in 2018, but Chakrabarti credits this initial partnership for Solugen’s entry into industrial manufacturing.
The proceeds from these early sales were reinvested into developing Solugen’s pilot-scale production capacity and preparing for a transition to industrial-grade chemical markets. In 2018, the company redeveloped an exploded chemical plant in Houston to build its first pilot plant. Two years later, in 2020, Solugen broke ground on its landmark Bioforge production facility in the same location as the pilot plant.
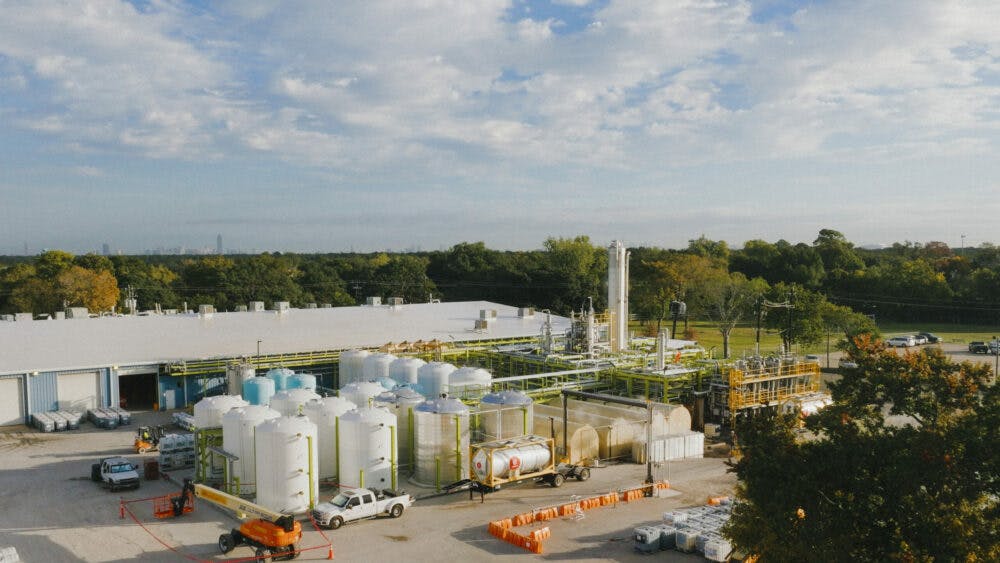
Source: Solugen
Product
Solugen has developed a vertically integrated platform combining enzyme engineering, metal catalysis, and software optimization to produce high-performance chemicals from renewable feedstocks. The process enables lower emissions, higher yields, and improved unit economics compared to conventional petrochemical methods. This platform is deployed through Solugen’s Bioforge facilities — modular plants designed for distributed manufacturing at industrial scale. As of March 2025, Solugen operates multiple sites and serves customers across the oil & gas, renewable fuels, aerospace & defense, agriculture, water treatment, construction, personal care, and cleaning industries.
Technology
Solugen’s core innovation lies in a hybrid manufacturing platform that combines biology and chemistry to produce high-performance, low-emission chemicals from renewable inputs. Rather than relying on fossil fuels and high-temperature petrochemical processes, Solugen’s system, called the chemi-enzymatic platform, combines engineered enzymes with metal catalysts, managed by proprietary software and optimized by machine learning.
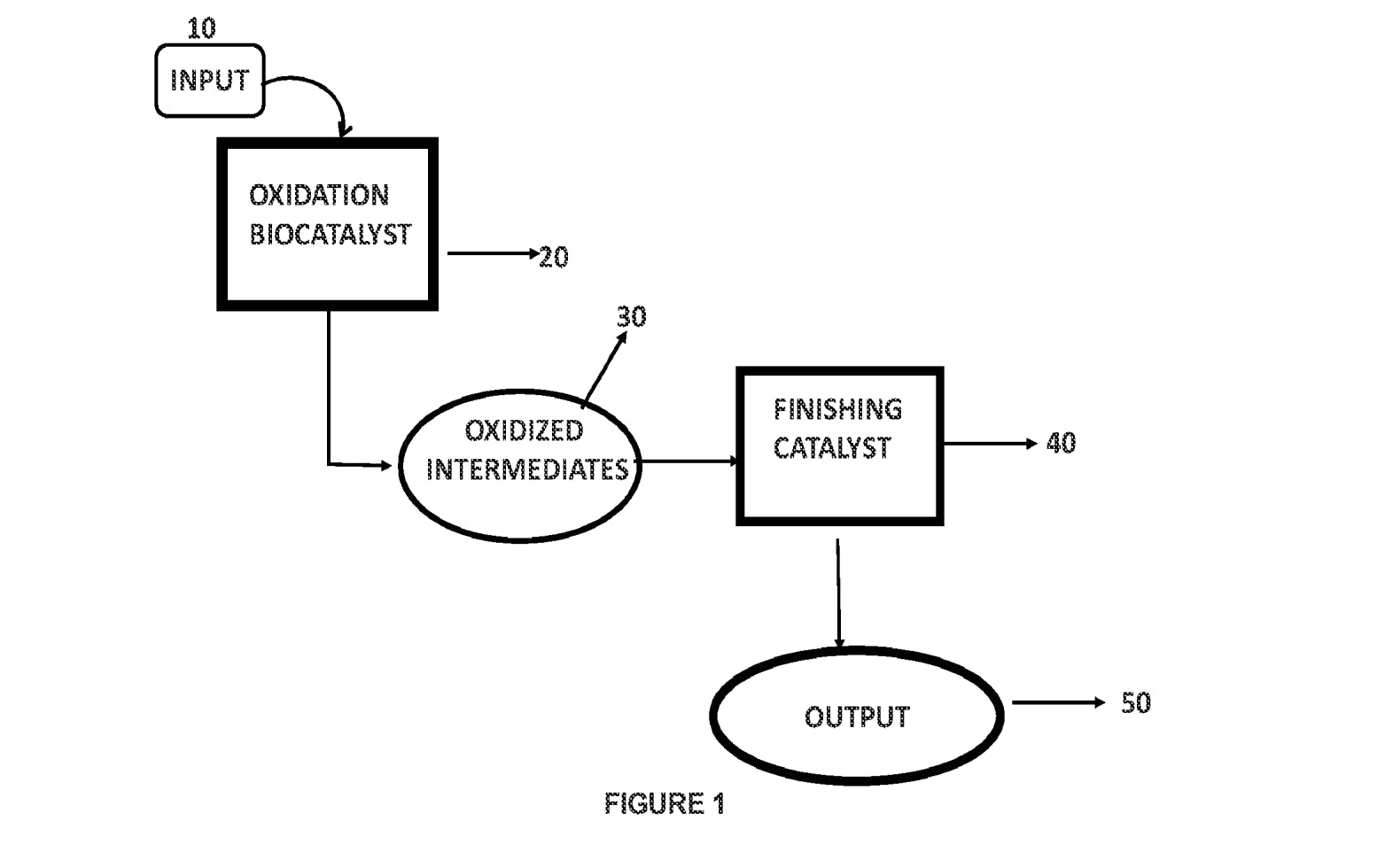
Source: WIPO
The process begins with a renewable feedstock, typically a mixture of dextrose, deionized water, and compressed air. This mixture flows into Solugen’s enzyme oxidation reactor, where custom-designed enzymes trigger specific chemical reactions under ambient conditions. These enzymes are genetically optimized through techniques like CRISPR-Cas9, high-throughput screening, and AI-guided modeling. Solugen uses both bacterial and fungal hosts to express enzymes, tailoring the expression system to each product’s requirements.
The partially converted solution then passes through a trickle-bed metal catalyst reactor. Metal surfaces, such as engineered gold catalysts, complete the transformation into the final chemical product. Where petrochemical yields often top out around 60%, Solugen has demonstrated commercial-scale yields of 95% or higher. Because the reactions run without combustion or extreme heat, the process generates no hazardous waste and consumes minimal energy, making it the first chemical production method to be certified as carbon-negative.
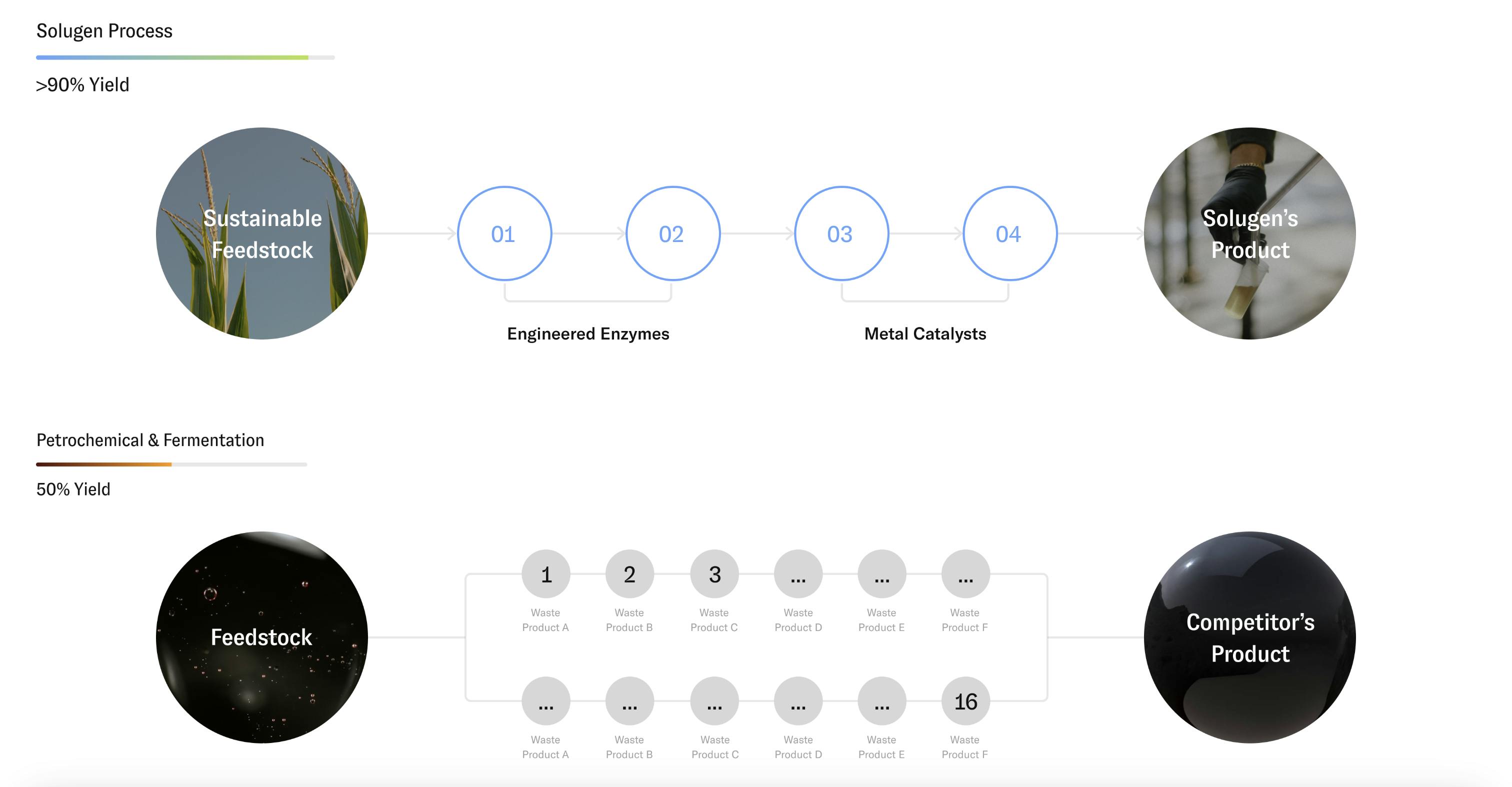
Source: Solugen
Software plays a central role in nearly every step of Solugen’s process. Internally developed machine learning models, such as Seq2Fitness and BADASS, accelerate enzyme development by predicting how specific mutations will affect performance. These tools reduce experimental cycles from seven rounds to one and shrink design timelines from 18 months to as little as three. Similarly, Bayesian optimization algorithms guide process development, helping engineers identify optimal reaction conditions with a fraction of the typical trial-and-error. In one case, software-guided experimentation reduced process costs by 60% with just 40 small-scale test runs.
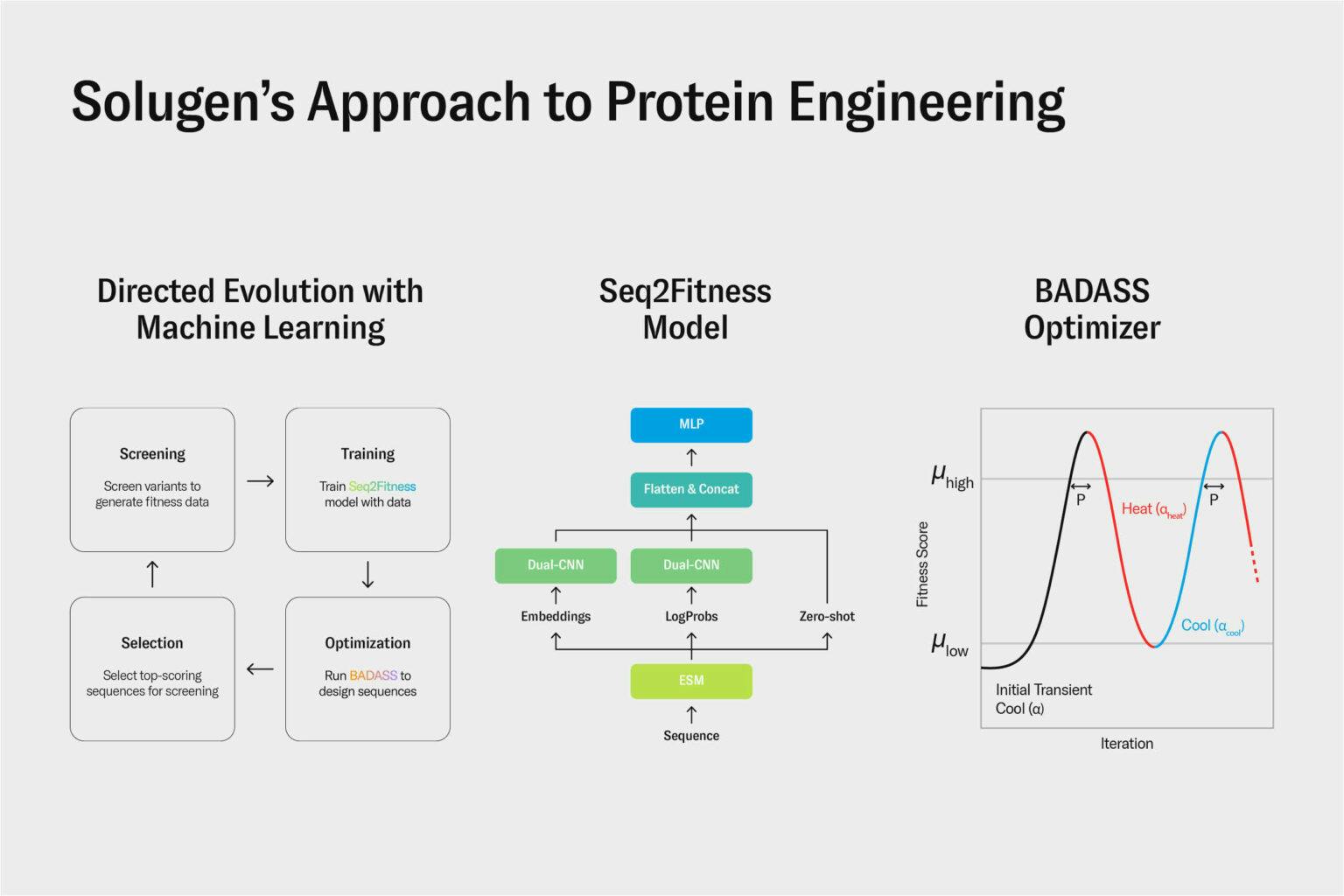
Source: Solugen
Software also underpins reactor control. Algorithms manage temperature, flow rate, and pressure across both enzymatic and metal-catalyst systems, ensuring consistency and throughput at industrial scale, running calculations through a Solugen server in Germany to figure out how to optimize the enzymes. To support this platform, Solugen has developed a set of technical capabilities in-house. Its teams span analytical chemistry, strain engineering, chemical synthesis, and fermentation. Equipment includes high-resolution instrumentation such as UPLC, GC, TOF-MS, and NMR. The company also maintains full QA/QC operations and a pilot plant for real-world testing.
Solugen’s core technology is protected by a growing patent portfolio, including filings covering multi-step oxidation processes that integrate biological and metal catalysis. These methods allow Solugen to convert substrates like glycerol or ethanol into value-added industrial compounds with lower emissions and higher selectivity than traditional chemical processes.
Facilities
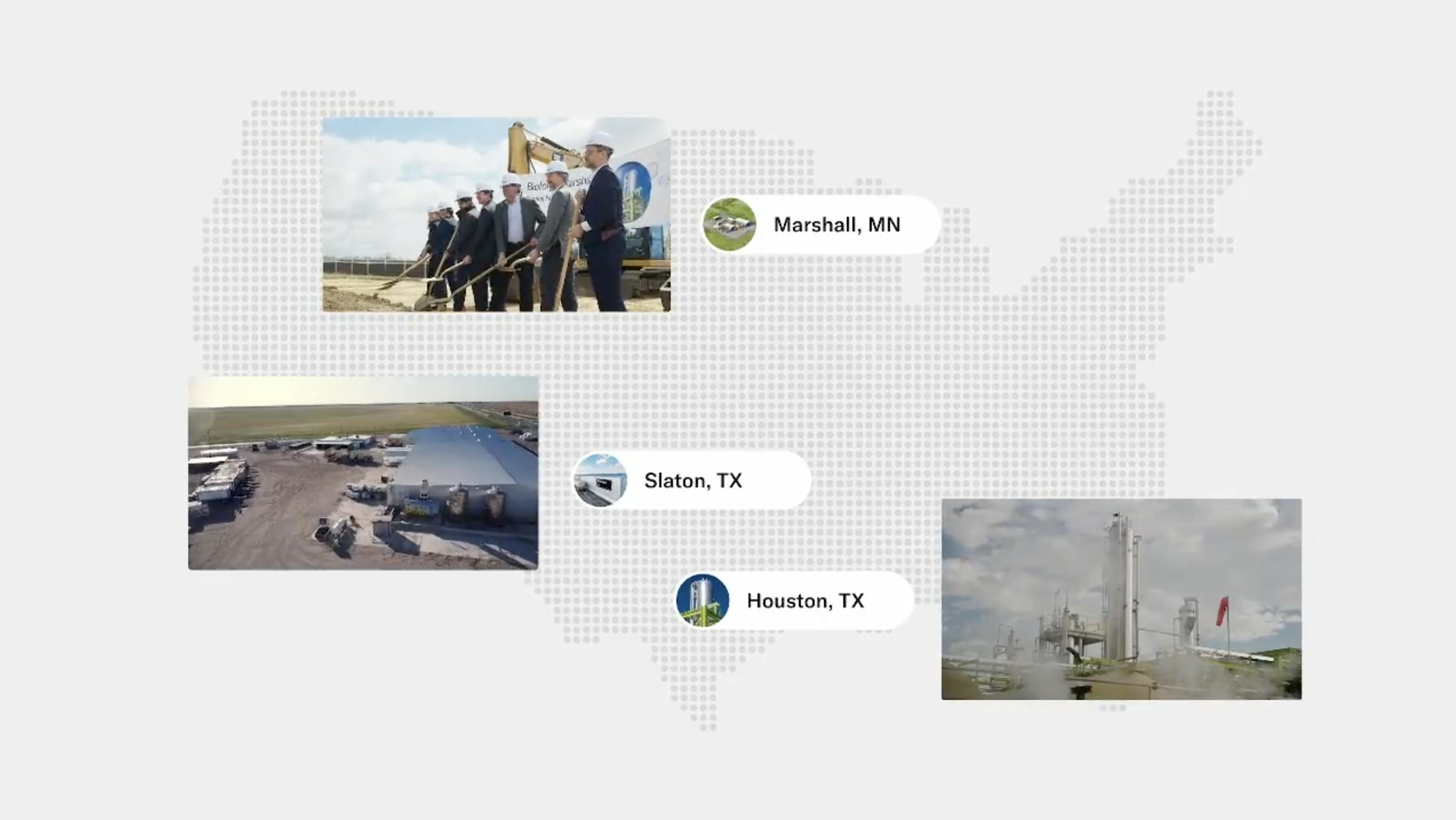
Source: X
Bioforge I – Houston, Texas
Solugen’s first full-scale biomanufacturing facility, Bioforge, was built on the site of a former chemical plant in Houston, Texas. Construction began after the company raised a $13.5 million Series A in 2018, following early traction from the wipes and float spa market. The facility became operational in 2021. Bioforge includes a 20K sq ft laboratory for research and development, a production plant with a 10K metric ton annual capacity, and a 10K sq ft warehouse. Bioforge is co-located with Solugen’s R&D team and serves as the company’s innovation hub. Baseline molecules and processes are developed and validated here before being transferred to other sites for scaled production.
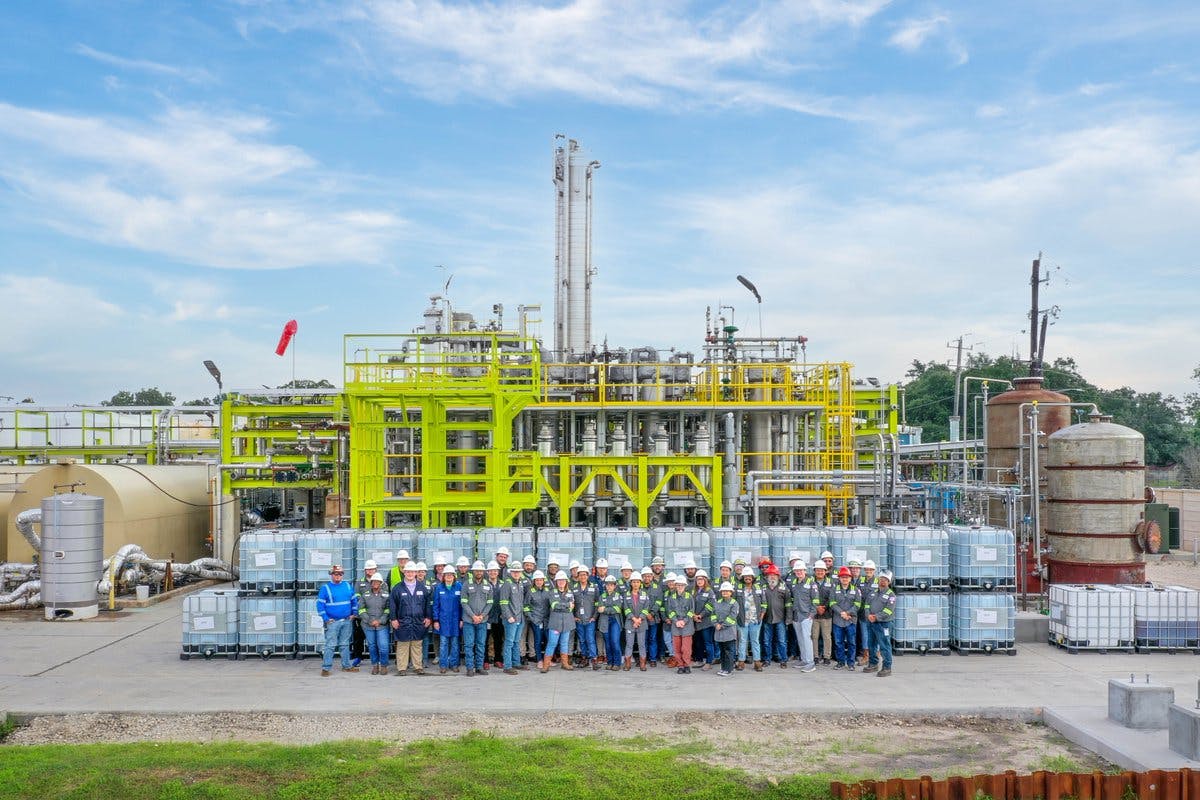
Source: X
Distribution Facility – Slaton, Texas
In 2019, Solugen established a 20K sq ft blending and distribution facility in Slaton, Texas. The location was chosen for its proximity to energy sector customers in West Texas. Chakrabarti pointed out that the facility was specifically set up to service produced water. It includes storage tanks, product blending capabilities, and logistics infrastructure to support the company’s growing list of industrial clients.
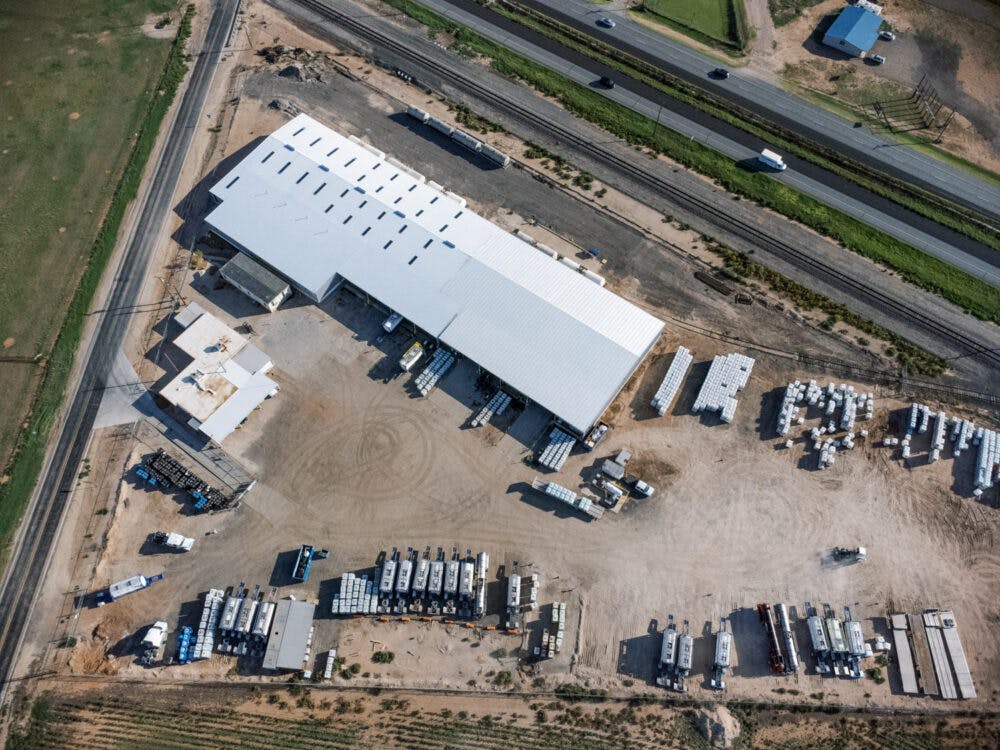
Source: Solugen
Bioforge II – Marshall, Minnesota
In April 2024, Solugen broke ground on its third production facility, Bioforge Marshall, located on a 34-acre site in Marshall, Minnesota. The 500K sq ft facility is being built adjacent to ADM’s existing corn processing complex as part of a strategic partnership. The project is backed by a $213.6 million conditional loan guarantee from the US Department of Energy — the same clean energy loan program used to fund Tesla’s Fremont factory.
At full capacity, Bioforge Marshall will convert approximately 150 million pounds of ADM-sourced dextrose annually into low-carbon organic acids for use in water treatment, agriculture, construction, personal care, and energy. Two pipelines will directly connect the facility to ADM’s plant, reducing transport costs and emissions. The facility is designed to house three modular production trains with a combined annual capacity of up to 120 kilotonnes.
Construction is expected to be completed by fall 2025. The plant will employ up to 100 temporary workers during development and over 50 permanent, high-skilled roles once operational. Solugen estimates that Bioforge Marshall will avoid 18 million kilograms of CO₂ emissions annually compared to traditional petrochemical and fermentation-based processes.
Bioforge II will serve as Solugen’s flagship scaled production site, enabling the company to expand its customer base while allowing the Houston-based Bioforge I to remain focused on research and new molecule development.
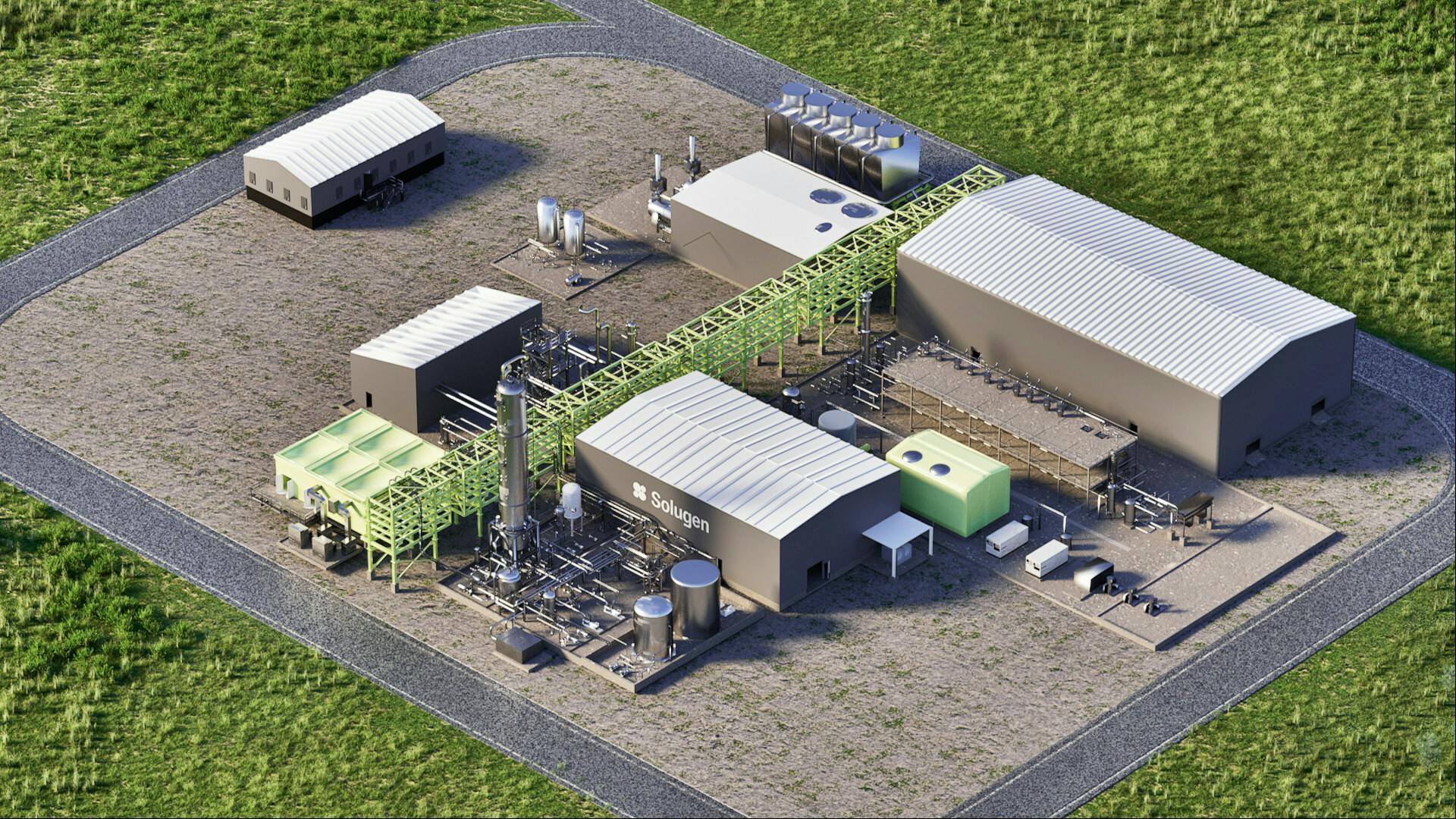
Source: PRN
Solugen plans to expand its Bioforge network across the US and internationally, enabling regional production of sustainable chemical inputs and further decentralizing traditional chemical infrastructure.
Solutions
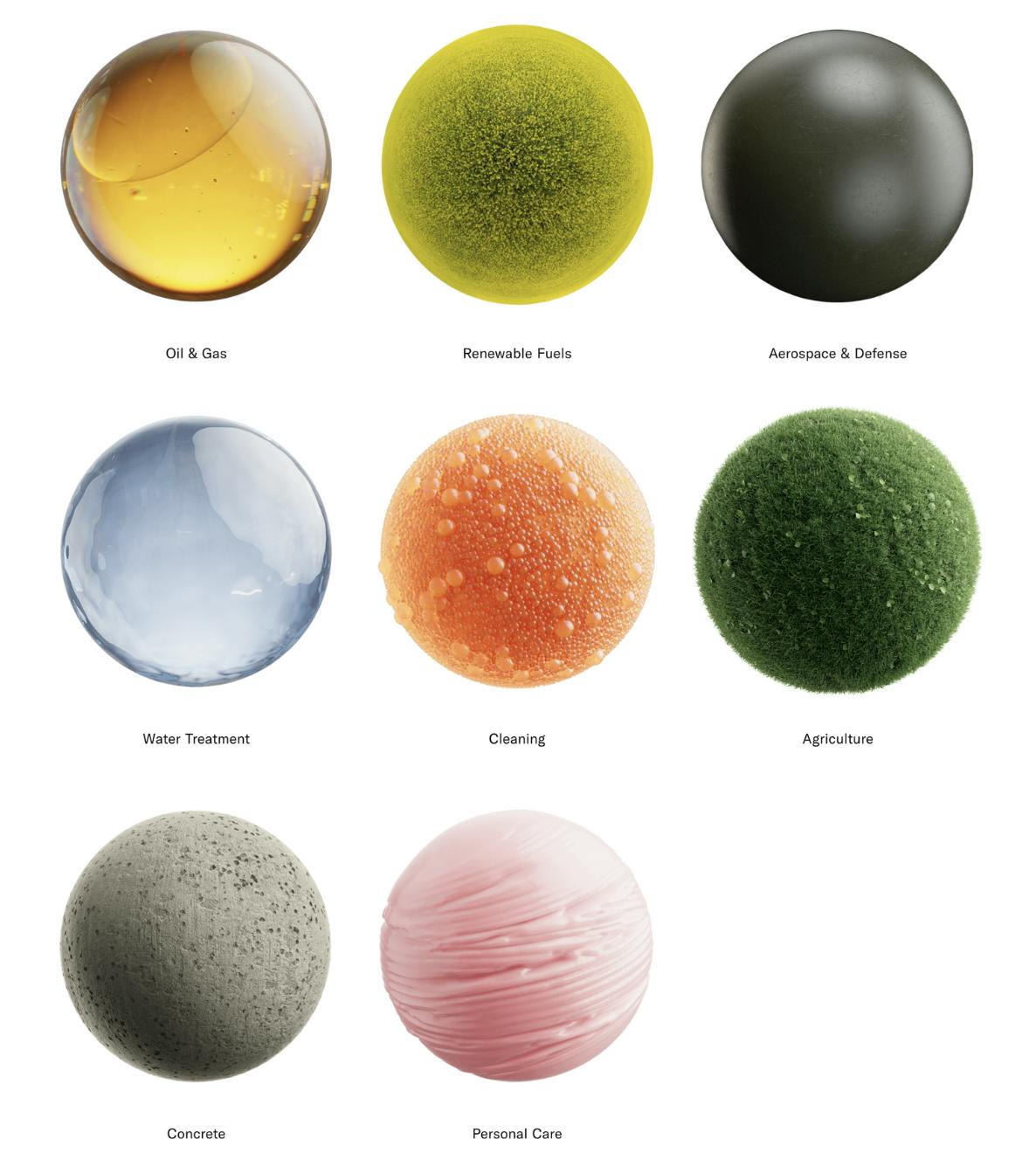
Source: Solugen
Solugen commercializes six distinct product lines, each tailored to a specific industrial segment. These product lines include Verza360, Altiv, Relox, NutriValent, AcquaCore, and TactiChem. All products are manufactured at Bioforge facilities, delivering performance on par with traditional petrochemicals while reducing carbon intensity and improving local availability.
Verza360: Solugen's Verza360 product line is a low-carbon chelating agent designed to remove metal ions in upstream and midstream energy operations. In saltwater disposal networks across Texas, Verza360 enabled operators to eliminate iron fouling and biofilm issues, reducing maintenance downtime and saving $2.6 million. In refining, the product has been used to degum biodiesel feedstocks and recover off-spec oil by removing 99% of iron content, improving yields and unlocking resale value. Verza360 replaces high-emission compounds like EDTA and THPS, offering carbon-negative performance with no compromise on effectiveness.
Altiv: Altiv contains organic acids and polyhydroxy acids (PHAs) used in consumer goods such as skincare, household cleaning, and sanitizing wipes. Designed to match the efficacy of legacy formulations, Altiv compounds demonstrate improvements in hydration and skin texture while maintaining a favorable environmental and toxicological profile. Solugen’s partnership with Sasol Chemicals includes evaluations of Altiv as a sustainable drop-in ingredient for surfactant systems.
Relox: Relox contains organic acid-based admixtures for concrete and cement applications. These additives help maintain strength and workability while reducing curing time and overall emissions. By eliminating fossil fuel-derived inputs, Relox offers a simplified supply chain and aligns with evolving environmental standards in the built environment.
NutriValent: NutriValent includes biodegradable complexing agents that enhance nutrient bioavailability in fertilizers and crop protection products. In field trials, NutriValent increased squash yields by 17% and improved drought resistance in crops exposed to variable watering schedules. These agents are fully compatible with existing formulations and have undergone third-party lifecycle assessments confirming their carbon-negative status.
AcquaCore: The AcquaCore product targets scale control, corrosion prevention, and microbial growth in municipal and industrial water systems. The line has been adopted by partners such as Kurita America to co-develop next-generation water treatment solutions for cooling towers. AcquaCore replaces hazardous phosphonates and carcinogenic additives with safer, bio-based alternatives, while offering performance equal to or better than incumbents.
TactiChem: Solugen's TactiChem product offering provides sustainable alternatives to imported or petroleum-derived materials used in defense and aerospace manufacturing. In 2023, Solugen received a contract from the US Department of Defense to scale bio-based critical inputs domestically. TactiChem’s solutions are designed to meet stringent performance and regulatory requirements while reducing exposure to geopolitical and environmental risks in the supply chain.
Market
Customer
As of March 2025, Solugen serves customers across the oil & gas, renewable fuels, aerospace & defense, agriculture, water treatment, construction, personal care, and cleaning industries. These customers typically operate industrial processes that rely on commodity chemicals such as chelating agents, corrosion inhibitors, organic acids, and surfactants. The supply chain for these chemicals is generally concentrated and relies on large, centralized suppliers.
In 2022, Solugen reported that it was servicing 30 customers and was on track to generate $100 million in revenue, implying an average annual order value of approximately $3.3 million per customer. The company’s customer base is diversified across industries and geographies, though its primary focus remains on mid-sized and large industrial operators. Notable examples include Kurita America, Diamond Wipes, Sasol Chemicals, and the US Department of Defense. Solugen also captured 80% of the floating spa market during its early go-to-market phase. Solugen believes its Bioforge platform could eventually produce up to 90% of the commodity chemicals used across the industry, as R&D and enzyme libraries expand.
Market Size
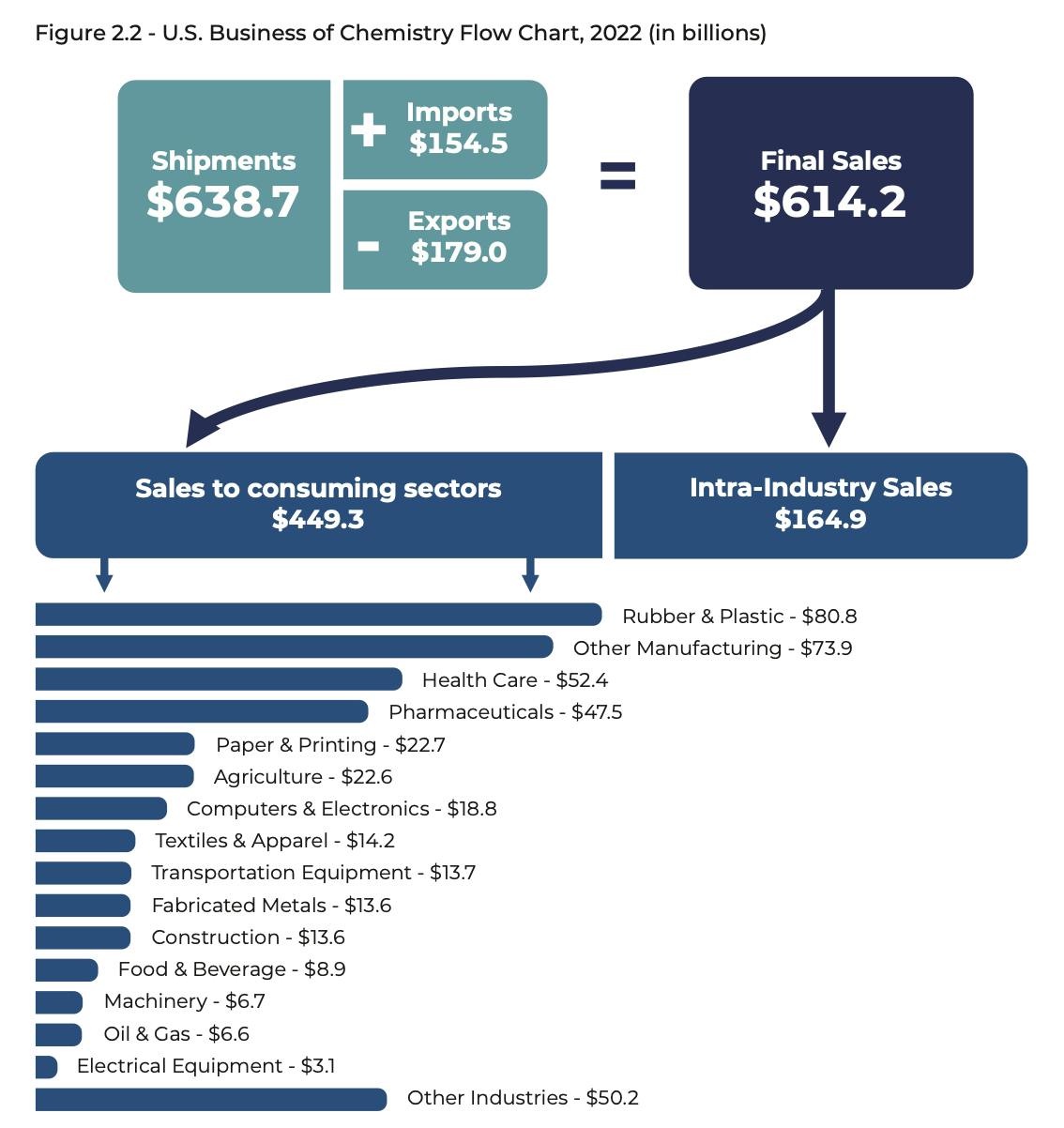
Source: American Chemistry
The global chemical industry was valued at over $6 trillion in 2025. In 2022, US chemical sales topped $600 billion, supporting the production of most commercial and household goods, contributing to 25% of GDP. In the same year, 13% of the world's chemicals came from the US. Solugen’s broader ambition is to decarbonize a large swath of commodity and specialty chemicals that today rely on fossil fuels and high-temperature processes.
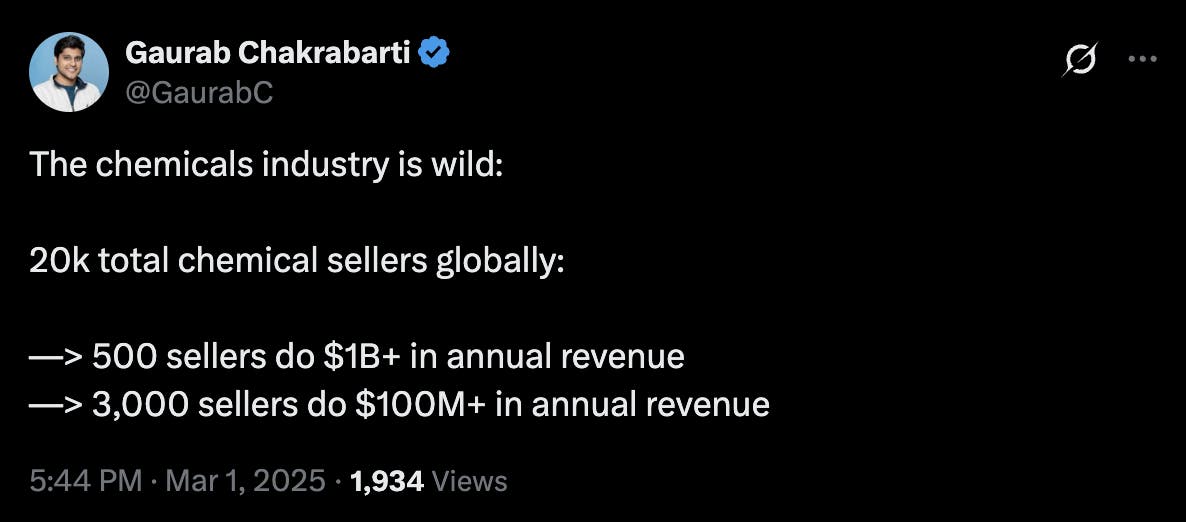
Source: Gaurab Chakrabarti via X
Competition
Ginkgo Bioworks: Founded in 2008 and based out of Boston, MA, Ginkgo Bioworks designs custom microbes for various applications, including the production of pharmaceuticals, agriculture, water treatment, and industrial chemical production. It uses genetic engineering and fermentation to produce sustainable chemicals. Gingko Bioworks works with some of the largest pharmaceutical companies in the world, including Pfizer, Boehringer Ingelheim, Novo Nordisk, Eli Lilly, and Moderna. Prior to going public in 2021, the company raised a total of $735 million from investors including T. Rowe Price, General Atlantic, and Viking Global Investors.
As of March 2025, its market cap was $410 million and the company was operating at a loss. In 2022, Ginkgo Bioworks acquired Zymergen, an ML/AI company studying and modifying microbes that produce chemicals, primarily for consumer goods and pharmaceuticals. After disclosing that it had difficulties scaling manufacturing and expanding sales, Zymergen’s stock had fallen almost 70% prior to its acquisition by Gingko Bioworks.
Twelve: Founded in 2015 and based in Berkeley, California, Twelve develops electrochemical reactors that convert captured carbon dioxide into chemical products traditionally derived from fossil fuels, including syngas, ethanol, and jet fuel. The company refers to its process as “industrial photosynthesis,” enabling carbon-neutral production of fuels and materials. Twelve has partnered with brands like Mercedes-Benz, Procter & Gamble and PG&E. As of March 2025, the company has raised $844 million in total funding from investors including DCVC, TPG, and SMBC. Its latest disclosed valuation was $1 billion in September 2024.
Lygos: Founded in 2010 and based in Berkeley, California, Lygos engineers microbes to convert plant-based sugars into high-value industrial chemicals, with a focus on applications where biology offers cost or performance advantages over traditional petrochemical processes. The company targets markets such as home care, personal care, agriculture, fragrances, and water treatment. Its product lines include Soltellus, a biodegradable polymer, and Ecoteria, a bio-based malonate used as a sustainable chemical building block. As of March 2025, Lygos has raised $211.5 million from investors including Y Combinator, the US Department of Energy, and LG Technology Ventures.
Monolith Materials: Founded in 2012 and headquartered in Lincoln, NE, Monolith Materials is a clean energy and chemicals company. Its main product focuses include carbon black (used in all car tires), black plastic, inks, batteries, and clean hydrogen (common in products such as fertilizers). As of March 2025, Monolith Materials has raised $364 million in funding from investors including Mitsubishi, TPG, and SK Group.
As of 2025, Monolith Materials is one of the world's largest producers of green hydrogen, a substance used in products such as fertilizer, and has the potential to be used as an energy source in the future. In mid-2022, Monolith Materials’ $1 billion manufacturing expansion broke ground. Its process uses traditional or renewable natural gas or biogas as the feedstock, which is superheated by renewable electricity to produce goods without CO2 emissions. As of March 2025, the company operates nine facilities across Nebraska, California, Colorado, and Kansas.
Mango Materials: Founded in 2010 and based in Vecaville, CA, Mango Materials is a biotechnology company that produces biodegradable plastics from waste methane gas, an abundant gas with few scaled uses. Methane is fed to bacteria which produces a biopolymer for harvesting. Because its plastics are biodegradable, Mango Material products do not contribute to plastic pollution. The biopolymer is sold to plastic producers for final good production. As of March 2025, Mango Materials has raised a total of $25.5 million from investors including Collaborative Fund, Freeflow Ventures, and Global Brain.
Novomer: Founded in 2010 in Rochester, NY, Novomer creates sustainable chemicals from waste carbon dioxide through proprietary catalyst technology for biodegradable products such as packaging, materials, adhesives, and metal coatings. Novomer was acquired by Danimer Scientific in July 2021 for $152 million.
Terramera: Founded in 2010 and focused on agriculture, Terramera develops plant-based products to replace chemical-based fertilizers and pest repellants. It combines robotics, targeted plant cells, and machine learning models to increase the efficacy of its insecticides, fungicides, and plant health products. As of March 2025, Terramera raised a total of $97 million in funding from investors including Ospraie Ag Sciences and the British Columbia Innovative Clean Energy Fund.
Business Model
Solugen generates revenue by selling high-performance, low-carbon chemical ingredients to industrial customers across sectors including oil & gas, renewable fuels, aerospace & defense, agriculture, water treatment, construction, personal care, and cleaning. Products are manufactured at the company’s Bioforge facilities and offered either as drop-in replacements for legacy inputs or as part of custom co-development partnerships.
While pricing is not disclosed publicly, Solugen positions its products as cost-competitive or lower-cost alternatives due to superior process efficiency, logistics advantages, and higher yields. In 2022, CEO Gaurab Chakrabarti stated that Solugen’s products achieved gross margins approached 60%, enabled by software-guided enzyme design, modular plant infrastructure, and conversion yields above 90%.
The company offers a tiered commercial model. For commodity inputs, Solugen sells directly or through exclusive distribution agreements for molecules like peroxides and citrates. For differentiated products, the company engages in multi-step partnerships — beginning with commercial goal alignment, followed by technical validation, and culminating in production agreements for new molecules or formulations.
Though capital-intensive, Solugen’s modular, co-located “mini-mill” model is designed to avoid the multi-billion dollar outlays typical of petrochemical megaprojects. By colocating near feedstock sources and end-users, Solugen reduces logistics costs, shortens time-to-market, and lowers emissions. However, scaling the Bioforge network will require significant capital investment and long-term operational discipline.
Traction
Solugen has scaled from lab-based R&D to commercial production, with meaningful revenue and a diversified customer base across multiple industrial sectors. In 2019, the company generated $12 million in revenue, primarily from energy and industrial customers in Texas. By 2022, Solugen was on pace for over $100 million in revenue across more than 30 active customers, equating to an average annual order size of $3.3 million. In 2022, Chakrabarti stated that most of Solugen’s products generated software-like gross margins of nearly 60%.
Adoption has extended across sectors including water treatment, agriculture, oil & gas, renewable fuels, aerospace & defense, construction, and personal care. Customers include Kurita America (co-developing water treatment solutions), Sasol Chemicals (evaluating bio-based drop-in replacements), the US Department of Defense (awarded a contract to secure domestic supply of critical inputs), and Diamond Wipes (an early partner in hydrogen peroxide-based sanitizing products). In the company’s earliest phase, Solugen captured 80% of the float spa market in the US. The company is also partnered with ADM, one of the world’s largest agricultural processors, to build Bioforge II and directly pipe in feedstock.
In April 2024, the company secured a $213.6 million conditional loan guarantee from the US Department of Energy - the same clean energy program that funded Tesla’s Fremont facility. Solugen’s cap table includes leading climate and growth investors such as GIC, Temasek, Lowercarbon Capital, Baillie Gifford, and Kinnevik AB. Kinnevik projects Solugen could reach $800 million in revenue by 2030 and describes it as the leading platform in the decarbonization of the $6 trillion global chemicals industry.
Solugen has received multiple awards for its innovation and impact, including CNBC’s Disruptor 50 2024 list, MIT Technology Review’s Climate Tech Companies to Watch in 2024, and Forbes’ inaugural list of Sustainability Leaders. In early 2025, Andreessen Horowitz named it in theAmerican Dynamism 50, a curated list of companies building critical national infrastructure.
As of 2025, Solugen is actively exploring international expansion. Swedish investor Kinnevik is supporting its entry into Europe, and the modular design of the company’s Bioforge plants is intended to enable decentralized, regional production closer to both feedstock and demand.
In March 2025, CEO Gaurab Chakrabarti was appointed to a three-year term on the Visiting Committee on Advanced Technology at the National Institute of Standards and Technology, under the US Department of Commerce. As part of VCAT, Chakrabarti will provide industry insights to help inform federal strategy on innovation, industrial resilience, and emerging technologies across sectors such as energy, defense, and AI.
Valuation
As of March 2025, Solugen has raised over $850 million in equity and debt financing. It raised a $213.6 million loan guarantee from the US Department of Energy in June 2024. Prior to that, Solugen raised a $200 million Series D in October 2022, led by Kinnevik, Lowercarbon Capital, and Refactor, following a $357 million Series C in September 2021 led by Baillie Gifford and GIC.
At the time of Solugen’s Series D round in October 2022, its post-money valuation was $2 billion and revenue was projected to reach $100 million, implying a 20x revenue multiple. As a proxy, Ginkgo Bioworks, LanzaTech, BASF, Ashland Global, and Eastman Chemical Company are comparable companies that are publicly traded.
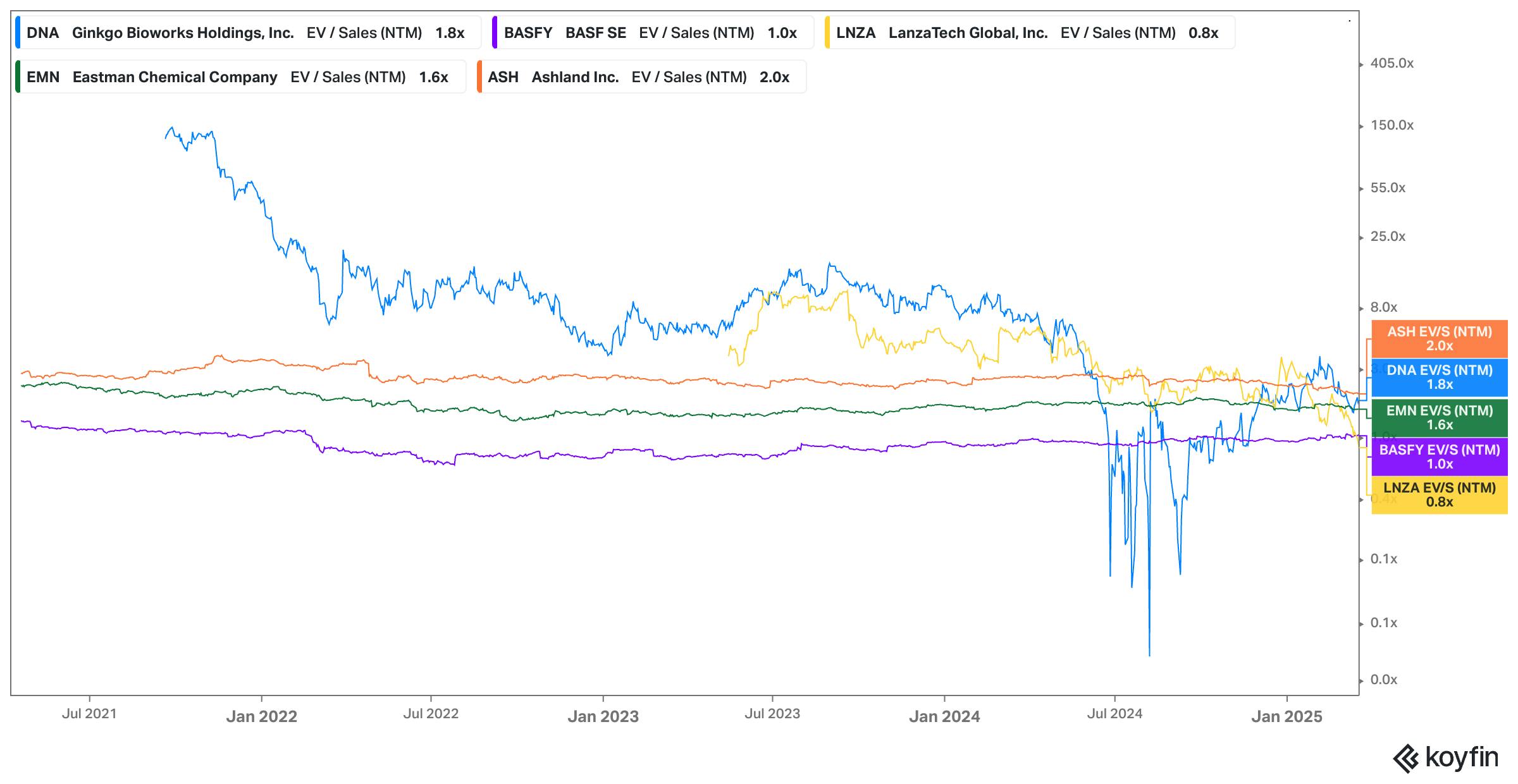
Source: Koyfin
Using these companies as a benchmark gives a range of revenue multiples: Ginkgo Bioworks at 1.8x, LanzaTech at 0.8x, BASF at 1.0x, Ashland Global at 2.0x, and Eastman Chemical Company at 1.6x.
As a growth-stage industrial biotech company with proprietary IP and vertically integrated manufacturing, Solugen’s implied 20x revenue multiple at the time of its Series D is significantly higher than those of mature public chemical and climate-tech peers, which range from 0.8x to 2.0x. This premium reflects investor confidence in Solugen’s platform scalability, carbon-negative economics, and early commercial traction. However, these multiples should be interpreted as a forward-looking signal, not a direct benchmark — Solugen’s valuation will ultimately be driven by its ability to scale Bioforge deployments, expand into new product verticals, and maintain high-margin unit economics across diverse industrial markets.
Key Opportunities
Distributed Biomanufacturing
Solugen aims to license its micromanufacturing technology to other chemical producers, enabling decentralized production of hydrogen peroxide and other bio-based chemicals. Rather than relying on large, centralized petrochemical complexes, the company is developing a model based on modular mini-mills — each capable of producing up to 5K tons of product annually. These facilities can be deployed closer to customers, reducing logistics costs and improving supply chain resilience. By building distributed plants within a 10-hour radius of end users, Solugen expects to reduce transportation emissions, shorten delivery times, and simplify compliance with local regulations.
Retrofitting Abandoned Factories
Solugen’s Houston Bioforge was built on the site of a former wax distillery that had exploded years earlier. By repurposing the site, the company qualified for substantial tax incentives and avoided the high costs of building from scratch — ultimately supporting higher margins. This model of retrofitting abandoned industrial infrastructure is core to Solugen’s expansion strategy. According to Chakrabarti, many deindustrialized regions in the US already possess the permitting, zoning, and utility infrastructure required for chemical manufacturing. Solugen sees these sites as opportunities to deploy its mini-mill model, while revitalizing economically depressed communities with new manufacturing jobs.
New Feedstocks
While corn syrup is Solugen’s primary feedstock, its enzyme reactors are designed to process a wide range of inputs - including simple sugars, alcohols, vegetable oils, and even recycled cellulose from cardboard. Longer term, Solugen is exploring the use of carbon dioxide as a direct feedstock through integration with carbon removal technologies. As of 2024, its reactors already remove significant CO₂ from the environment — up to 30K tons per 10K tons of product.
New Solutions
Solugen is actively expanding its molecular pipeline beyond current offerings, with ongoing R&D focused on new applications in personal care and food & beverage. The company aims to enter higher-volume markets by developing bio-based alternatives for plastics, amines, glycols, and other foundational chemistries. These categories represent a significant share of global chemical demand and offer a clear path for Solugen to scale its impact and revenue across both consumer and industrial sectors.
Regulatory Pressure
Responsible for nearly 25% of global emissions in 2021, the industrial sector has been under scrutiny to reduce environmental impact for some time. Around the world, governments are attempting to force industries to reduce their emissions through carbon pricing, renewable energy incentives, emission standards, R&D funding, sustainable procurement policies, green building standards, and more. The US Department of Energy released the Industrial Decarbonization Roadmap in 2022, which lays out plans to reduce emissions across iron and steel, chemicals, food and beverage, petroleum refining, and cement production. If positioned well, Solugen may be able to ride the tailwinds of government regulation targeted at chemical producers and consumers (those using the chemicals), which may have the effect of increasing demand for Solugen’s offerings.
Key Risks
Competition
Solugen operates in a space where competition is intensifying from two directions. On one side, incumbent petrochemical players possess existing infrastructure, scale advantages, and pricing power. On the other, a wave of synthetic biology startups, including companies like LanzaTech and Lygos, are targeting similar end markets. As these players mature, Solugen could face downward pricing pressure or accelerated commoditization.
Intellectual Property
Solugen’s competitive moat depends on the strength of its intellectual property, including patents on its chemi-enzymatic production process and enzyme designs. As more startups and corporates enter the bio-based chemicals space, there is a risk of IP infringement or legal disputes over overlapping methods. Additionally, delays in patent approvals or restrictions on key technologies could slow R&D and limit addressable markets.
Government Policy
Although climate policy has provided strong tailwinds for sustainable manufacturing, changes in the political landscape could pose risks. The rollback of federal climate initiatives or clean energy funding programs under a new administration may limit access to government-backed loans, tax credits, or procurement opportunities. Solugen’s reliance on financing partners, such as the Department of Energy, which issued a $213 million conditional loan guarantee for the Bioforge Marshall facility in April 2024, makes the company partially vulnerable to regulatory shifts. The Biden-era DOE Loan Programs Office announced 53 deals totaling about $107.6 billion in financial commitments. As of February 2025, $60.2 billion of these loans have been finalized and $47 billion remain conditional.
Summary
Solugen’s mission is to “de-fossilize the chemicals industry” by replacing traditional petrochemical processes with enzyme and metal catalyst-based alternatives. Sean Hunt initially viewed enzymes as unreliable, but advances in machine learning have enabled Solugen to extend enzyme lifespans from minutes to weeks. Looking ahead, Solugen envisions a shift from operating its own production facilities to licensing its chemi-enzymatic Bioforge technology. Chakrabarti compares the opportunity to asset-light platform models like Airbnb or Uber, asking, “What if we’re the largest chemical company, but don’t own any chemical assets?”
Whether this transition can unlock the next phase of growth, and whether Solugen can maintain defensibility as others enter the bio-based chemicals space - remains to be seen. But the ambition is clear: to become the backbone of a decentralized, carbon-negative chemical industry.