Thesis
Quality is a critical aspect of any manufacturing process and consumer experience. The 2016 Samsung recall of 2.5 million units of the Galaxy Note 7 cost $5.3 billion because the batteries were heating up and causing fires. As of January 2024, product development costs thousands of dollars and months of labor, but those costs are exacerbated by failed quality control. Costs of poor quality include costs associated with rework, scrap, and warranty claims and can range from 15% to 40% of a company’s total operations.
In medicine, the first step to diagnosing a problem in a patient's body is a computed tomography (CT) scan or MRI. However, this type of diagnostic overview hasn’t historically been used by most quality control labs. Instead, such labs often employ outdated methods, such as destructively cutting products in half with band saws and calipers.
Product designers and manufacturers today face a similar challenge to doctors in the past. They often need to determine whether prototypes or production samples contain internal defects, and industrial CT scanners, or industrial computed tomography scanners, are powerful tools for non-destructive internal inspections. However, these machines are prohibitively expensive and complex, costing between $300K to $2.1 million, accessible primarily to large, well-funded companies.
Meanwhile, the ongoing digital transformation in manufacturing, sometimes referred to as "the Fourth Industrial Revolution", has meant that companies are integrating more advanced technologies like AI, machine learning, and real-time data analytics into their production lines. The rise of smart factories, which utilize automation and data-driven decision-making, has accelerated the adoption of cutting-edge scanning technologies in manufacturing. By enabling manufacturers to obtain detailed 3D images and data from a single scan, industrial CT scanning allows for the early detection of defects.
Beyond quality control, such scans can be used to optimize entire manufacturing processes through data analysis. Predictive analytics in quality control allows manufacturers to anticipate how changes in materials or processes will affect product quality. By analyzing real-time data, predictive models can flag potential quality issues before they occur, allowing manufacturers the opportunity to adjust operations automatically to prevent defects.
This approach not only improves the production process but also generates valuable data on the manufacturing lifecycle of each product. Over time, collecting and analyzing this data can lead to the creation of extensive databases of manufactured items, allowing companies to gain insights into production trends, quality patterns, and optimization opportunities. As a result, quality control can be used as a stepping stone toward building a comprehensive database that can drive improvements across industries.
This is where Lumafield comes in. Lumafield provides low-cost industrial CT scanners called Neptune and Triton, and a companion browser-based CT analysis system called Voyager. As the global population grows and the required output of manufacturing increases, the need for affordable, non-destructive quality control methods with greater efficiency will become more prevalent. Lumafield has claimed that it can provide a quality control solution to smaller manufacturers at over a 50% discount to traditional industrial CT scanners.
In a September 2024 interview with Contrary Research, Lumafield CEO Eduardo Torrealba described the company's vision for reaching its full potential: using data from scans to help progress toward fully automated manufacturing that leverages AI. As he explained in the interview:
“We really started this company because we want to build the organization that can take [us] from humans in the loop for designing manufacturing to humans out of the loop…. An AI model is not going to be able to design something if it doesn’t understand design knowledge, and that’s not information that’s available on the open internet. It’s not going to be able to manufacture something if it doesn’t understand all of the world’s manufacturing knowledge, another thing that’s not available on the open internet. So we wanted to build a company that is the source of truth of data for all of manufacturing… [and] we looked at the landscape of all the things you can do in manufacturing and [concluded that] the best quality data that you could possibly generate in manufacturing are CT scans.”
Founding Story
Lumafield was founded in 2019 by Eduardo Torrealba (CEO), Andreas Bastian (Head of Product), Kevin Cedrone (Head of R&D), Scott Johnston (Head of Engineering), Ric Fulop (Chairman), and Jonathan Aharon (Head of Operations & Finance).
Before founding the company, the team worked on design and fabrication technologies at companies like Formlabs and Autodesk. That experience gave them insight into what “engineers are capable of when you give them access to powerful but intuitive tools to supercharge their design processes.”
In particular, the founders’ experience going between first sketches and mass manufacturing made clear to them that there was “a major gap in the product development process”, namely that “while products and fabrication technologies had become more complex and sophisticated, the debugging tools that engineers used to solve their design problems were stuck in the 19th century.”
In seeking a solution to this problem, Lumafield’s founders began by asking questions like: “What if you could diagnose problems with assemblies immediately? What if you could find invisible cracks that would otherwise lead to huge product recalls? What if you could understand changes in manufacturing lines over time?” These questions led them to start the company that would become Lumafield.
Initially, the company (which was known as Meter) was in stealth, despite raising its seed round in 2019 and its Series A in 2020 from investors like Lux and Kleiner Perkins.
“We’ve tried to stay under the radar as we’ve developed all of this amazing technology. We did so because we wanted to be able to focus on the hard parts of the challenge first. Our team has an allergic reaction to hype. We didn’t wait until we had built the first working scanner to announce our work—we waited until we had shipped multiple revisions of our products to dozens of paying customers.”
In April 2022, the company emerged from stealth and made its funding and new company name public.
Product
Why Lumafield Began with CT Scanners
Based on his past experiences, Lumafield CEO Eduardo Torrealba realized that “you couldn’t perfect design without understanding manufacturing” and vice versa; as a result, he “wanted to link those two things together.” As a result, Lumafield chose to start with CT scanning services because, in the company's view, CT scanning provides the “best quality data you could possibly generate in manufacturing.”
Lumafield’s team saw an opportunity to modernize CT scanning by making it more affordable and easier to use while embedding it directly into the everyday workflows of engineering and manufacturing organizations. However, the company's vision went beyond improving existing CT technology. In a September 2024 interview with Contrary Research, Torrealba described the company's approach as follows:
“We looked at the entire thing. There’s the actual scanner itself. There’s the fundamental technology that acquires the images, and there’s all the electronics, compute, and software. We decided we wanted to be vertically integrated. We wanted to design our own scanners, build our own X-ray detection technology, run our own factory, [and] build our own software from scratch.”
This allowed Lumafield to create a product that could be seamlessly integrated with a company’s broader design and manufacturing data, offering a “nucleation point” for the rest of the manufacturing process: by making its technology affordable and easy to integrate into daily operations, Lumafield aims to embed itself into the workflow of engineering and manufacturing organizations.
This is intended to enable companies to not only improve their quality control but also use the collected data as a foundational point for broader insights into design and manufacturing. Essentially, Lumafield wants to become the central hub for all the design and manufacturing data companies generate, offering a comprehensive, accessible resource that supports innovation and efficiency across their processes. Lumafield’s goal is to position itself to address the entire manufacturing lifecycle and build a database of industrial knowledge.
How Industrial Scanners Work
The workings of an industrial CT scanner can be likened to solving a Sudoku puzzle. In Sudoku, the missing numbers are deduced with the understanding that the numbers in a row, column, and box meet specific requirements to be considered complete.
Similarly, industrial computed tomography scanning involves capturing multiple 2D X-ray images, or radiographs, from all angles around an object. Each of these radiographs provides an X-ray shadow. This shadow reveals the internal features encountered by the X-ray as it passes through the object to the detector. This information is then reconstructed through a sophisticated algorithm much like using context clues to piece together a Suduko puzzle.
During the reconstruction process, the X-ray shadows are analyzed and combined to map out the distribution of materials within an object in three dimensions. The result is a detailed 3D image where each “voxel,” a 3D pixel, represents the material density at a specific point within the object. This non-destructive technique allows engineers and manufacturers to examine an object’s internal and external structures, without compromising its physical integrity.
Unlike traditional 2D X-ray imaging, industrial CTs generate an image with complete 3D volume, presenting a holistic view of the object. This process enables the user to view any part of the object from any angle, offering a detailed inspection capability that surpasses conventional methods. CT scanning can be used for both traditionally manufactured parts as well as complex parts that are produced by additive manufacturing (or 3D printing).
However, the CT scanner is only one component. The true productivity of CT scanning is unlocked when integrated with software tools for visualization and analysis, enhancing its potential across various industry applications. Lumafield offers a suite of products that address both parts of the equation — the hardware and the software — including Voyager, Atlas, Triton, and Neptune.
Voyager
Voyager is Lumafield’s cloud-based inspection platform that runs directly in a web browser. It enables users to visualize, analyze, and share CT data from any computer, regardless of their location. It can be used to consolidate data from industrial CT scanners or 3D surface scanners.
Data and Attributes Panel
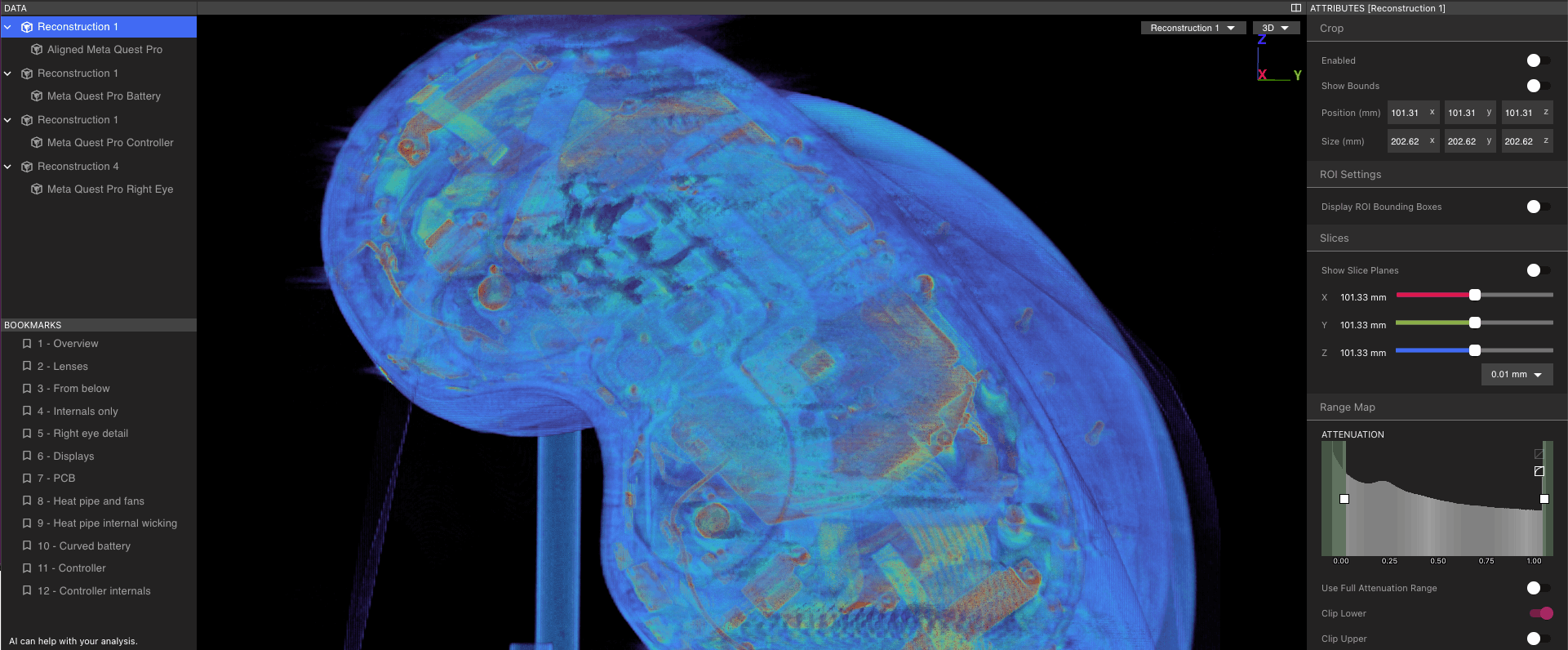
Source: Lumafield
The data tab, found on the left of the data and attribution panel, contains scan and project information. Data can include information on reconstruction, radiographs, porosity, CAD comparisons, and more. Attributes found on the right are adjustable parameters directly associated with the data. These attributes include options for cropping, controlling the slice, adjusting the view, setting the range, managing color mapping, and altering opacity.
Lumafield’s range and color mapping feature determines how the raw reconstruction is translated into colors and intensities on the screen. Typically, the left-most peak in the histogram represents the scan background (air), while the peaks to the right correspond to different materials. By adjusting the sliders, users can change the range of intensity values mapped to the selected color palette. Lowering the lower bound removes the background while reducing the upper bound decreases the display of high-intensity material. Additionally, users can adjust the color map values for finer control over scene visualization.
The data and attributes tabs are interconnected, ensuring that any changes made to the attributes are immediately reflected in the data with the goal of providing a seamless and responsive user experience.
Slice Views
Source: Lumafield
As the name implies, this feature provides a view of a slice of a reconstruction. Similar to how a standard medical CT visualization looks, these are reconstructions of a slice across a 3D object on cardinal axes.
Bookmarks
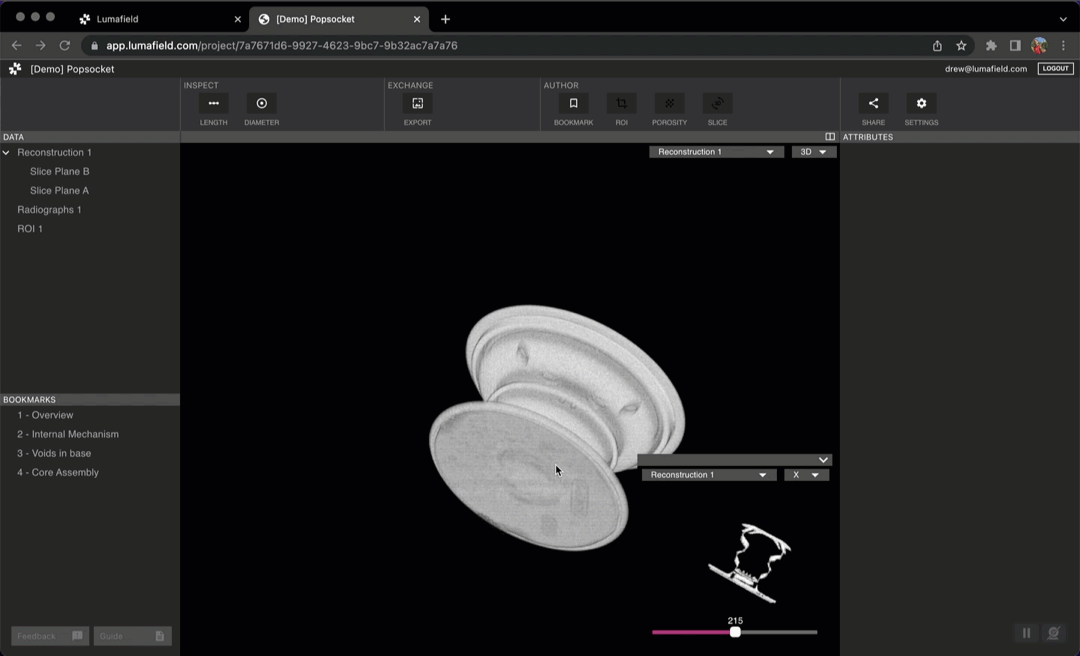
Source: Lumafield
Within Voyager, a user can bookmark the different views that they are analyzing. The bookmarks appear in the bottom left tab and, on selection, will show a comment thread on the right. This allows bookmarks to be a means of communicating ideas with peers and users viewing the project. These comments will populate live, so if two users view a project concurrently, they can communicate in real time.
Inspection Planes
This feature enables users to analyze what is happening on a 2D slice of a product. Once a user selects a reconstruction and selects the inspection plane button, a new inspection plane data object is created.
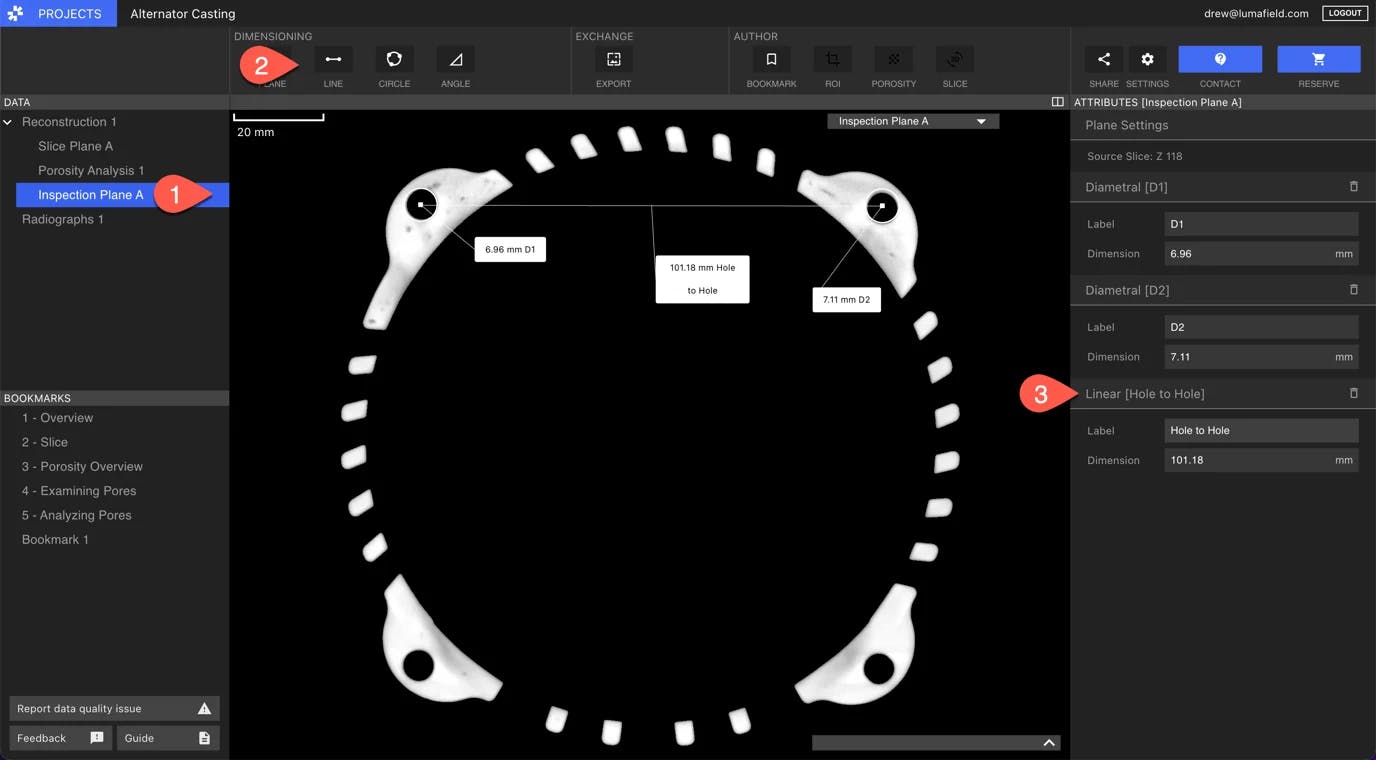
Source: Lumafield
Lumafield’s dimensioning tools include options for drawing circles, lines, and angles, each labeled for clarity. A line can be created with two points, a start and end point. A circle is defined using three points along its perimeter. For an angle, four points are used: two for each line that forms the angle. The label’s location determines what angle is being measured.
Auto Alignment
After two meshes have been coarsely aligned with the manual manipulation handles, the auto alignment tool allows a user to snap the meshes into alignment based on the globally calculated best alignment.
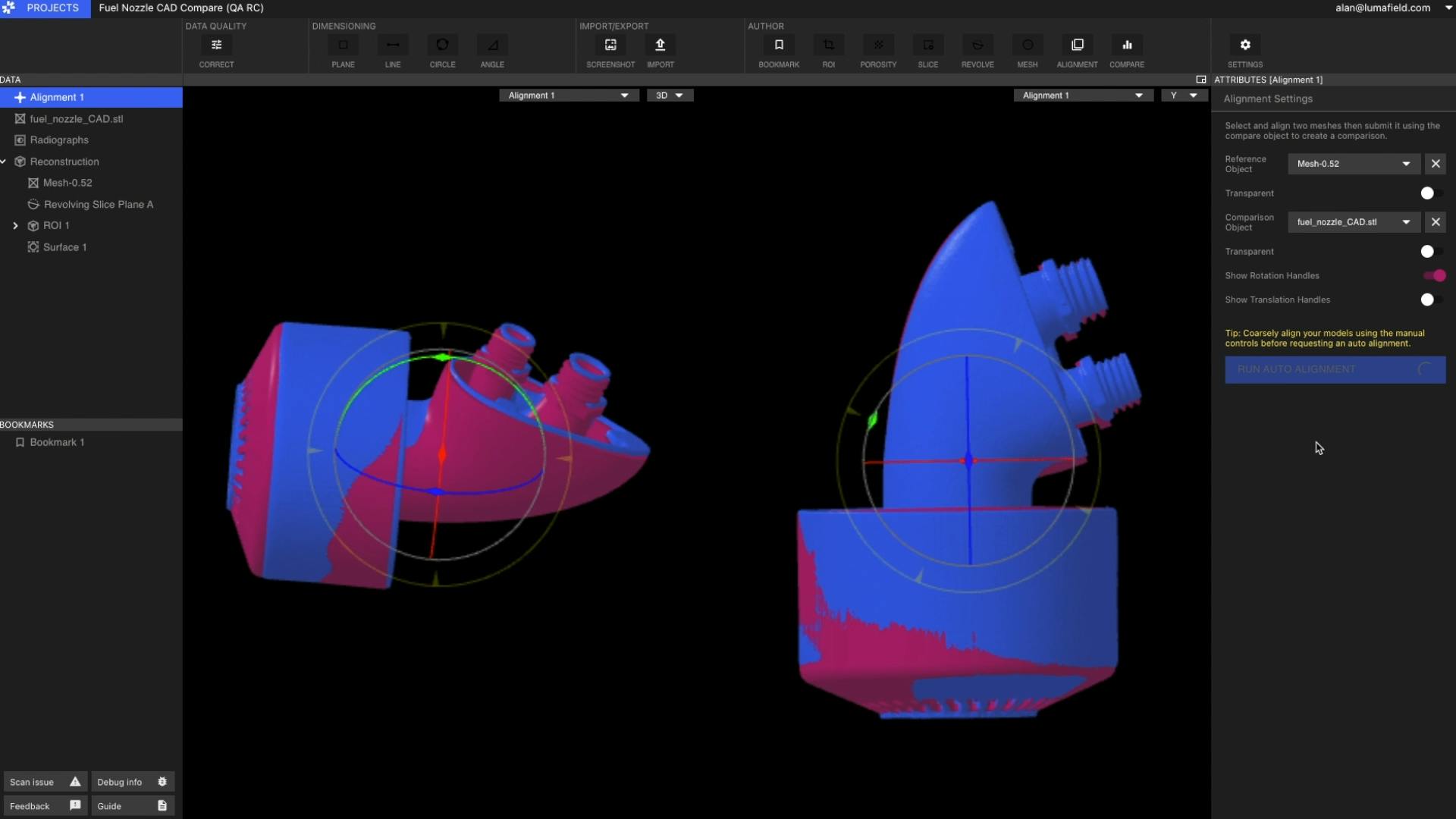
Source: Lumafield
In this view, the pink and blue represent two separate parts of the same model. The blue is a mesh of a printed part, while the pink is an STL file. Auto alignment allows for a precise set of deviations between the STL and the mesh to help a user understand where there are differences between the intended and resulting outcomes. This can also be applied to two meshes. These alignments can be used on either computer-aided design (CAD) comparisons, digital files that contain a 2D or 3D model of physical objects, or scan-to-scan comparisons.
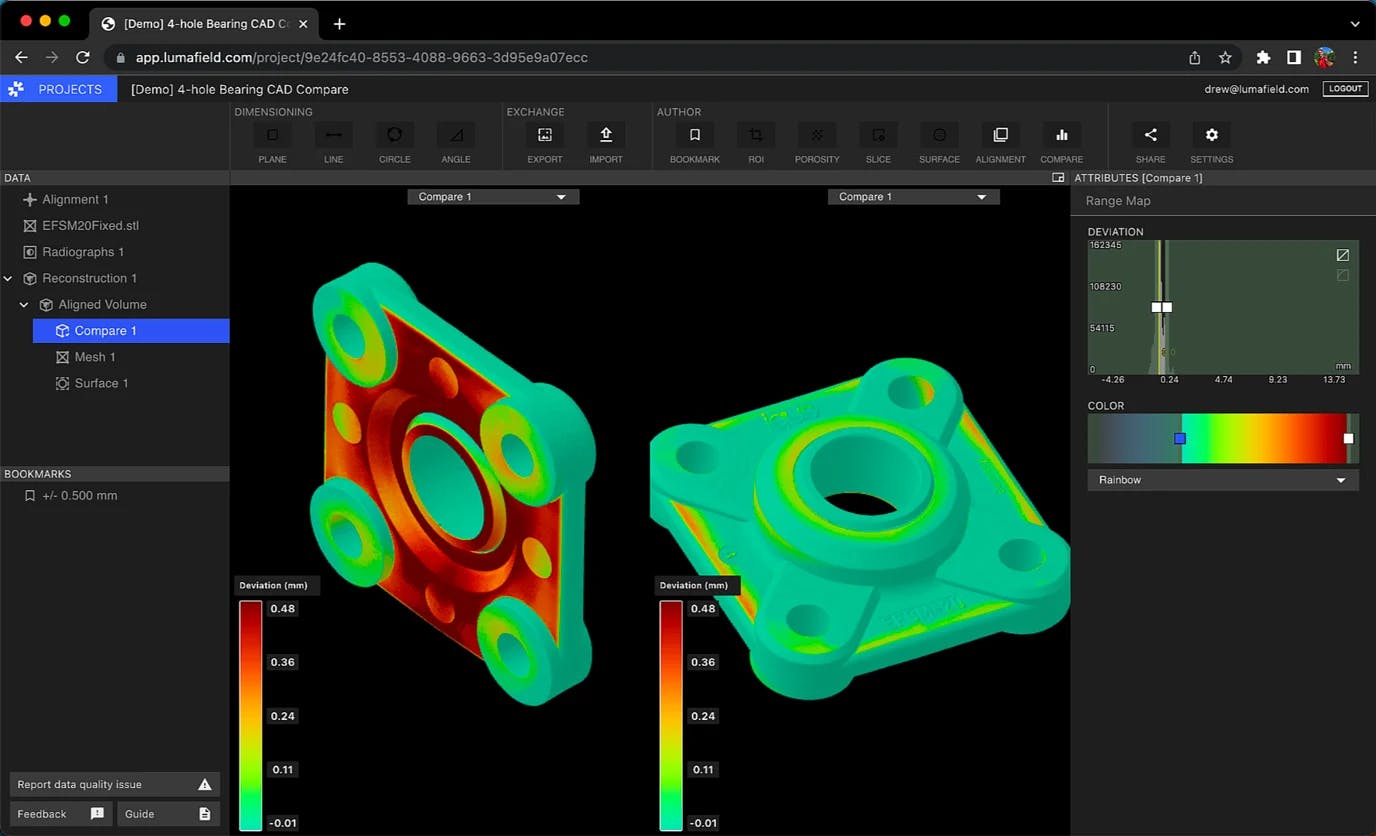
Source: Lumafield
For CAD comparison workflow, after the alignment is made between two pieces, a user can select “compare” from the top bar. This creates a new object under the alignment object. Once the comparison is complete, a range map and color map selector are provided. The range map on the right enforces tolerance ranges, while the color map is used to draw attention in specific ways.
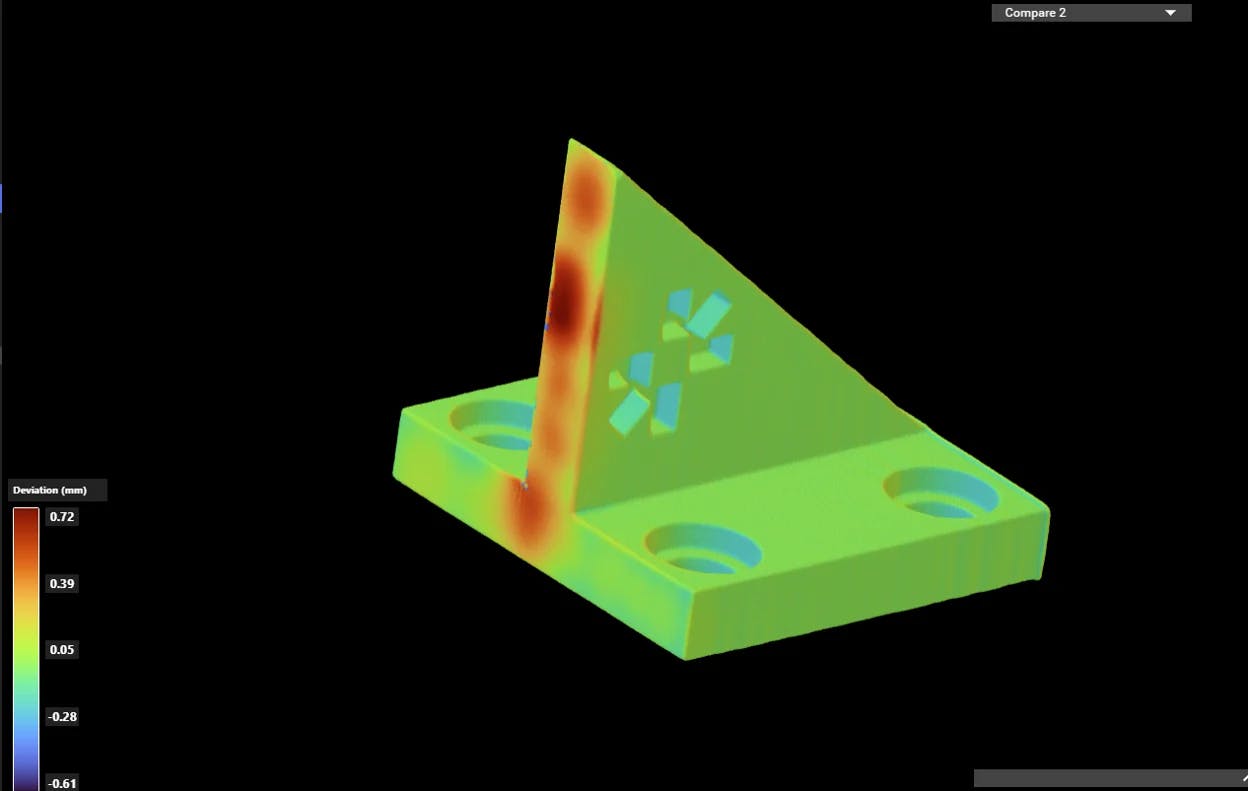
Source: Lumafield
A scan-to-scan comparison is effectively the same thing as the CAD comparison but between two scans from a CT scanner. The scan-to-scan comparison is meant to be a deviation check between two products in manufacturing. This feature provides an understanding of whether manufacturing equipment is facing wear and tear and how it may impact the product. These capabilities turn complex analyses into a straightforward check, shortening iteration cycles, and maintaining product quality across a line.
Custom Slice Planes
Custom Slice planes allow a user to define slice planes beyond X-Y-Z planes. A user would select the reconstruction or element that they want to place the slice plane on and select the slice tool. This will bring them to a view where the user can set up rotation and translation to focus on the feature of interest. The slider on the right window functions in the same way by allowing a user to navigate slicing through a particular part of a product. The axis length can also beadjusted for more granular control.
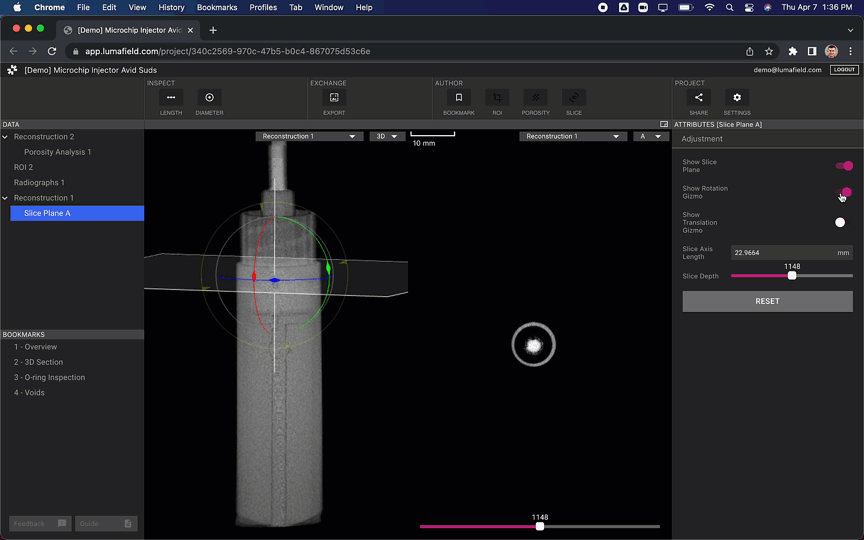
Source: Lumafield
Revolving Slice Planes
Revolving slice planes allow a user to set up a plane on the X, Y, or Z axis that rotates 360 degrees through the scan. A user would select an item to create the revolving slice plane, then create a 3-point circle to define the diameter. Once submitted, a Slice Angle Slider on the right data panel would allow a user to rotate through the part. The center of the diameter defined earlier acts as a pivot point for the rotation. These are particularly useful to inspect seals for possible leakage, assembly analysis for tubing, fittings, and valves, or analyzing the threads of a screw.
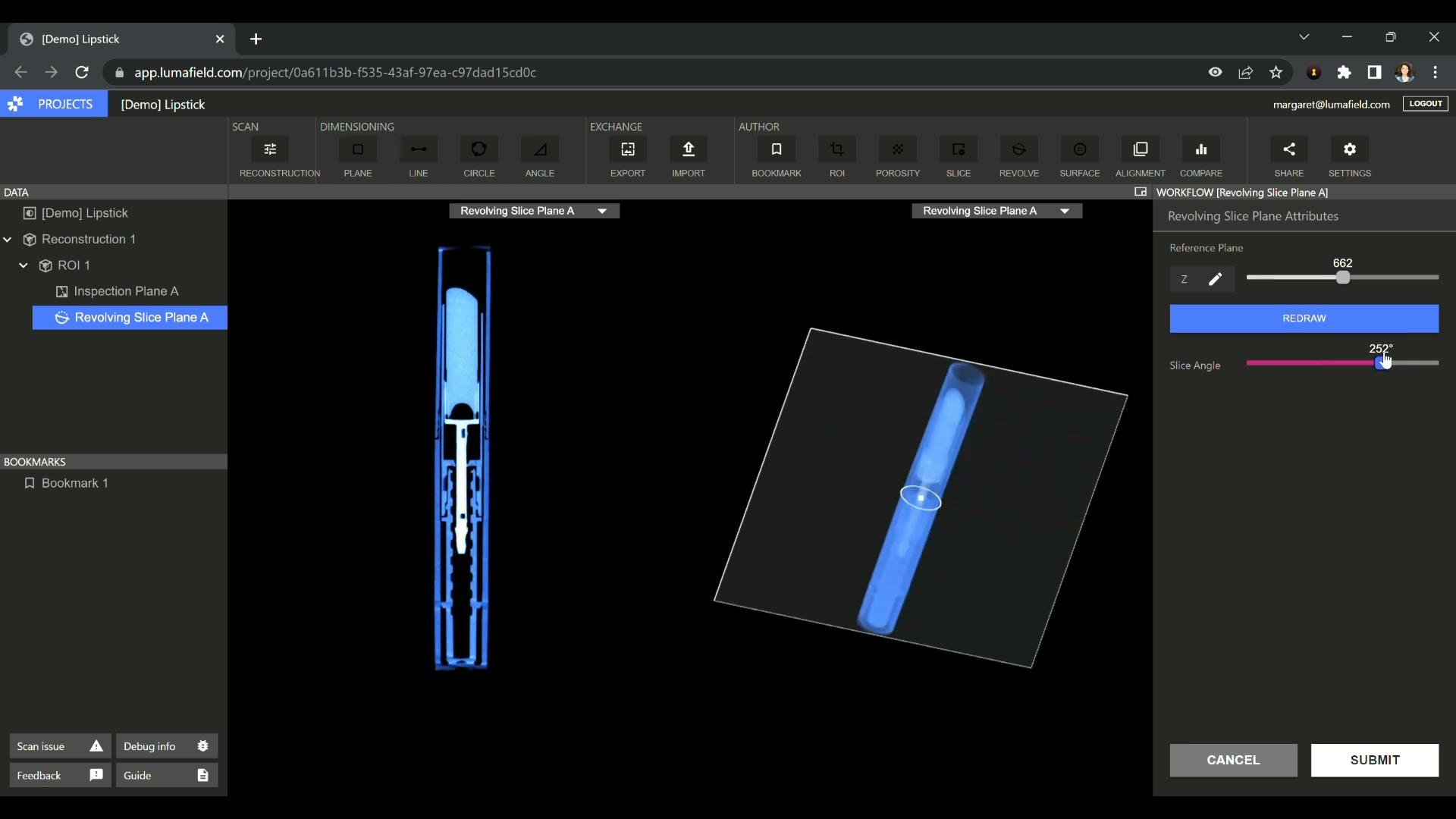
Source: Lumafield
Region of Interest
This feature allows a user to zoom into specific areas of the scan. By zooming in, it allows regions to be excluded, while also bringing chaining tools into a workflow. The region of interest tool allows users to align the scan to a specific, user-defined coordinate system, enhance the resolution of specific areas of the scan, and enhance contrast by removing high or low-density materials. It is important to note that the region of interest tools can be nested upon each other.
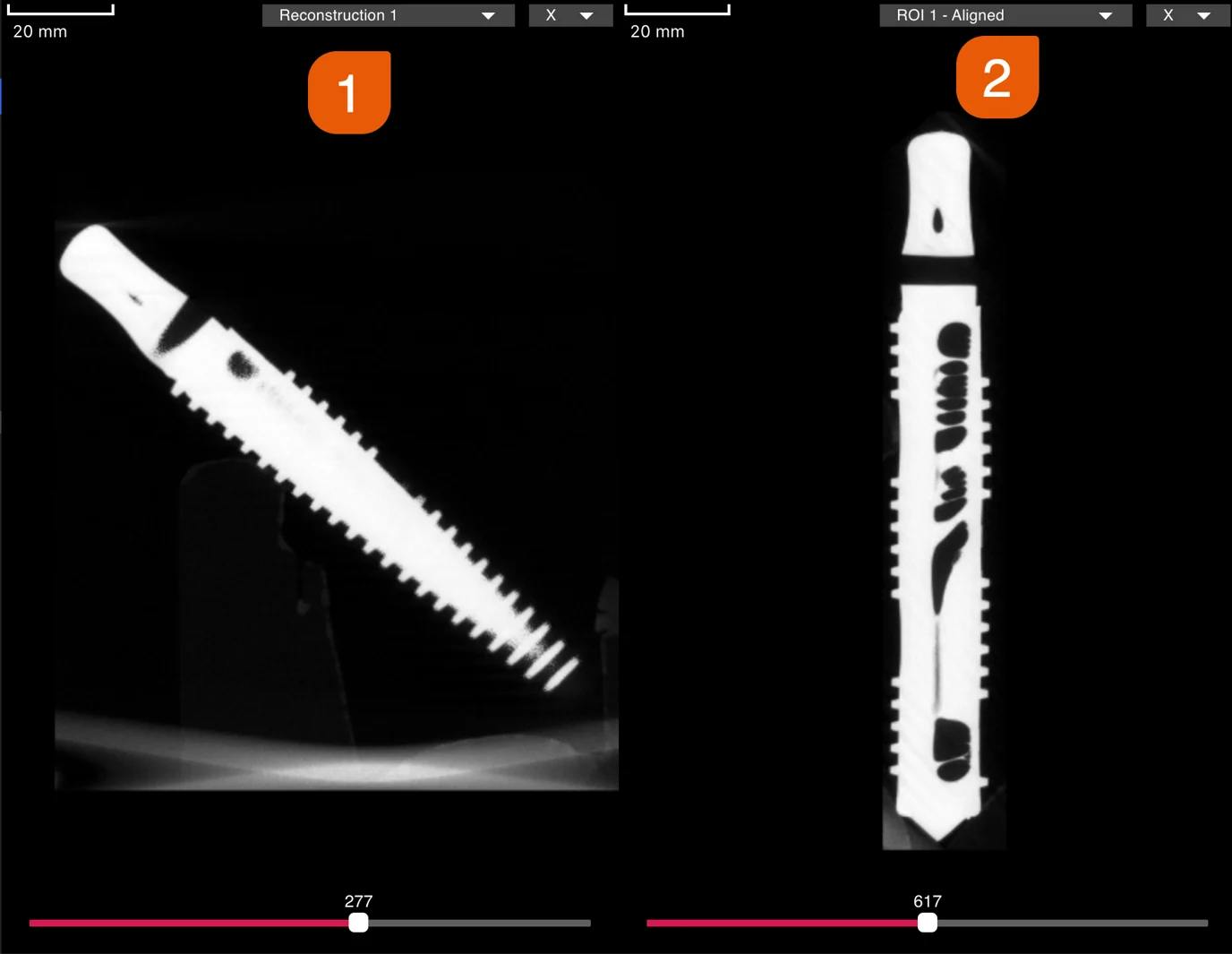
Source: Lumafield
Porosity
The porosity tool detects voids and pores that compromise material integrity and lead to part failures. Porosity can also lead to fractures. Being able to analyze whether there are pores in an object reduces the likelihood of part failure. Porosity canlocate where leakages in packaging could occur. In terms of real effects, this could mean product spoilage, contamination, reduced shelf life, and compromised safety.
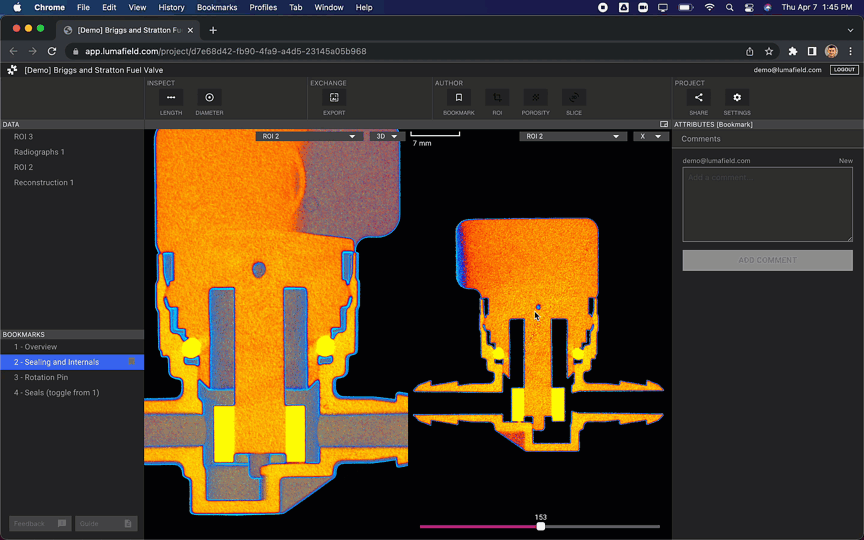
Source: Lumafield
The porosity tool enables a user to save and run an analysis on porosity with a custom pore threshold size.
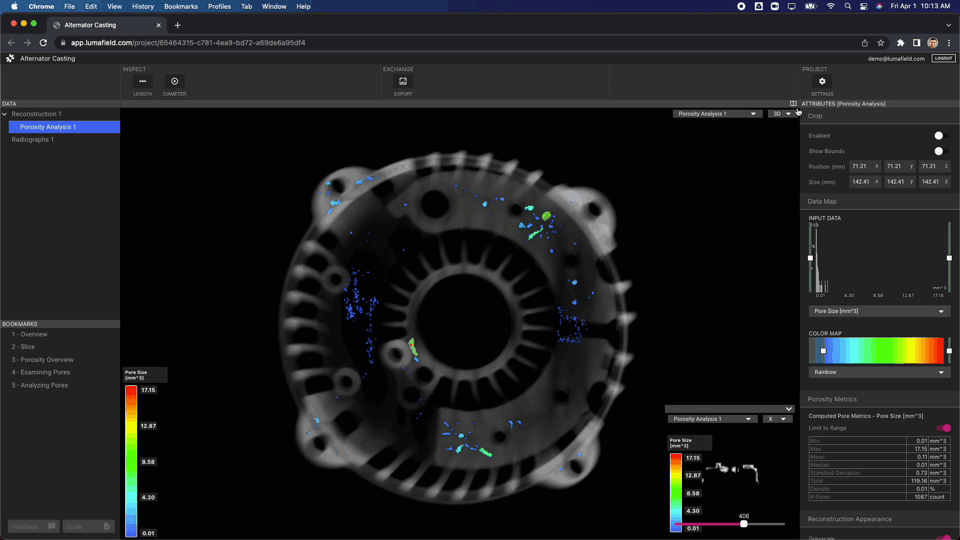
Source: Lumafield
When the porosity analysis is completed and loaded, it appears under the reconstruction tab. This analysis tool also provides metrics to the user to explain the nuances of the pores that are being addressed. This can be seen on the right tab under Pore Metrics.
Mesh Smoothing
Creating a mesh from volumetric data involves segmenting the data into different groups to identify distinct materials. Voyager supports binary segmentation, the process of partitioning a digital image into multiple segments to simplify or change the representation of an image into something more meaningful and easier to analyze.
Binary segmentation involves separating the data into two distinct groups. During segmentation, artifacts or noise can cause inaccuracies at the boundaries, resulting in high-frequency, low-amplitude noise on the mesh surface. Artifacts are distortions or errors in the image that do not originate from the actual scanned object, and noise refers to random variations in the image signal. Mesh smoothing can address this surface noise, making the mesh more representative of the real object.
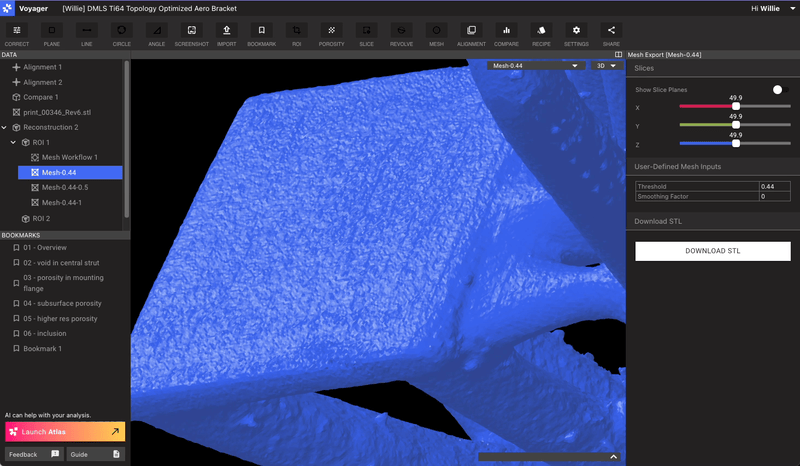
Source: Lumafield
While smoothing may reduce accuracy in specific areas like creases or corners, it generally improves overall mesh quality and should be used carefully to enhance meshing results.
Renormalization
Renormalization in CT scanning enhances the perception of details within multi-material scans by adjusting specific ranges of attenuation values. Volumetric data, stored as a cube of voxels, will store more voxels than can be displayed in Voyager with more depth in color.
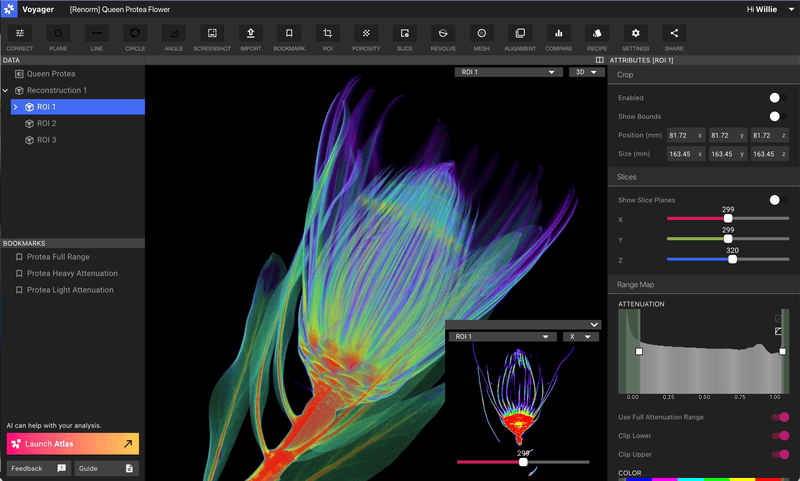
Source: Lumafield
Within the region of interest tooling, a user can access the renormalization feature. This feature has three options:
Default Range: This is the default applied to scans once they have been created.
Selected Range: These are the specific values that the range mapper and visualization show. This can be used when choosing a specific range to normalize the ROI
Full Range: If the default data looks like it has been clipped, which can happen with high variation multi-material datasets, this will allow access to raw, unclipped data.
Crack Detection & Analysis
The crack detection tool is used to identify and analyze cracks, leaks, surface pits, and surface-connected voids. Cracks refer to fractures, fissures, or discontinuities within a material often caused by structural failures, impact damage, or wear and tear over time. Surface voids and pitting appear as small, localized depressions or cavities on a material's surface. These voids typically result from deterioration, corrosion, mechanical damage, or manufacturing process issues. Leaks refer to unintended pathways through which a substance, such as a fluid or gas, escapes from a sealed or contained system due to improper design, manufacturing defects, damage, or wear.
To access this feature, the user must have access to the integrity analysis module within Voyager. A user can utilize this feature by selecting a reconstruction tool and then “cracks” in the top toolbar. This will prompt the user to set a crack threshold and the cracks can then be seen in 2D slices (X, Y, and Z views). Cracks in blue are more likely to be detected. A user can also define a max crack diameter for detection in conjunction with the measurement bar in the viewer.
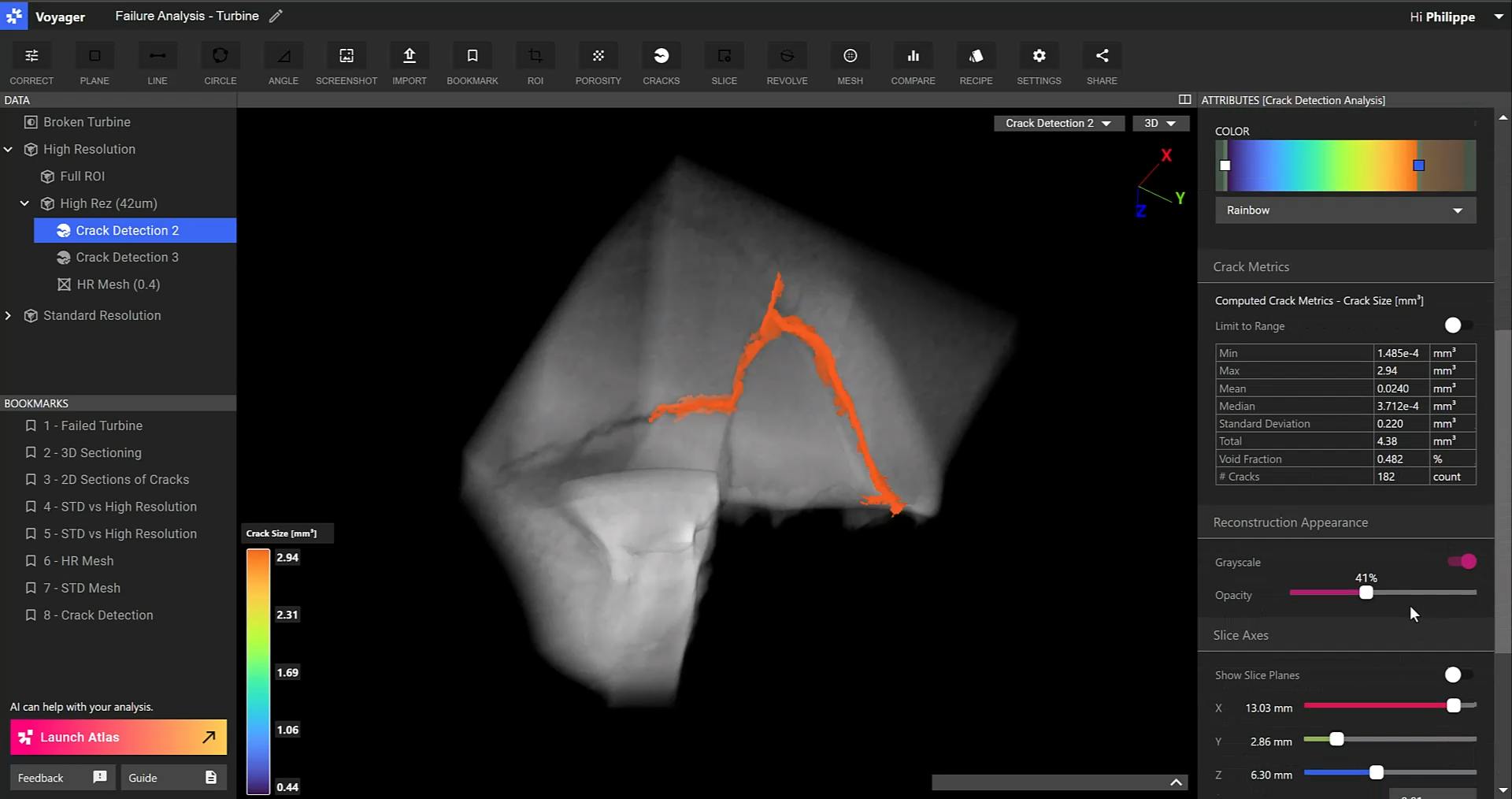
Source: Lumafield
This process is similar to the porosity analysis, as are the results. Cracks are highlighted when adjusting the range map. Once Voyager has run crack detection, the analysis will appear under the volume that it was run upon in the data panel.
Beam Hardening Correction (BHC)
BHC is used to correct beam hardening artifacts and reduce streaking artifacts in the software. This panel can be seen on the right once clicking the correct button in the toolbar, and turning on the BHC option.
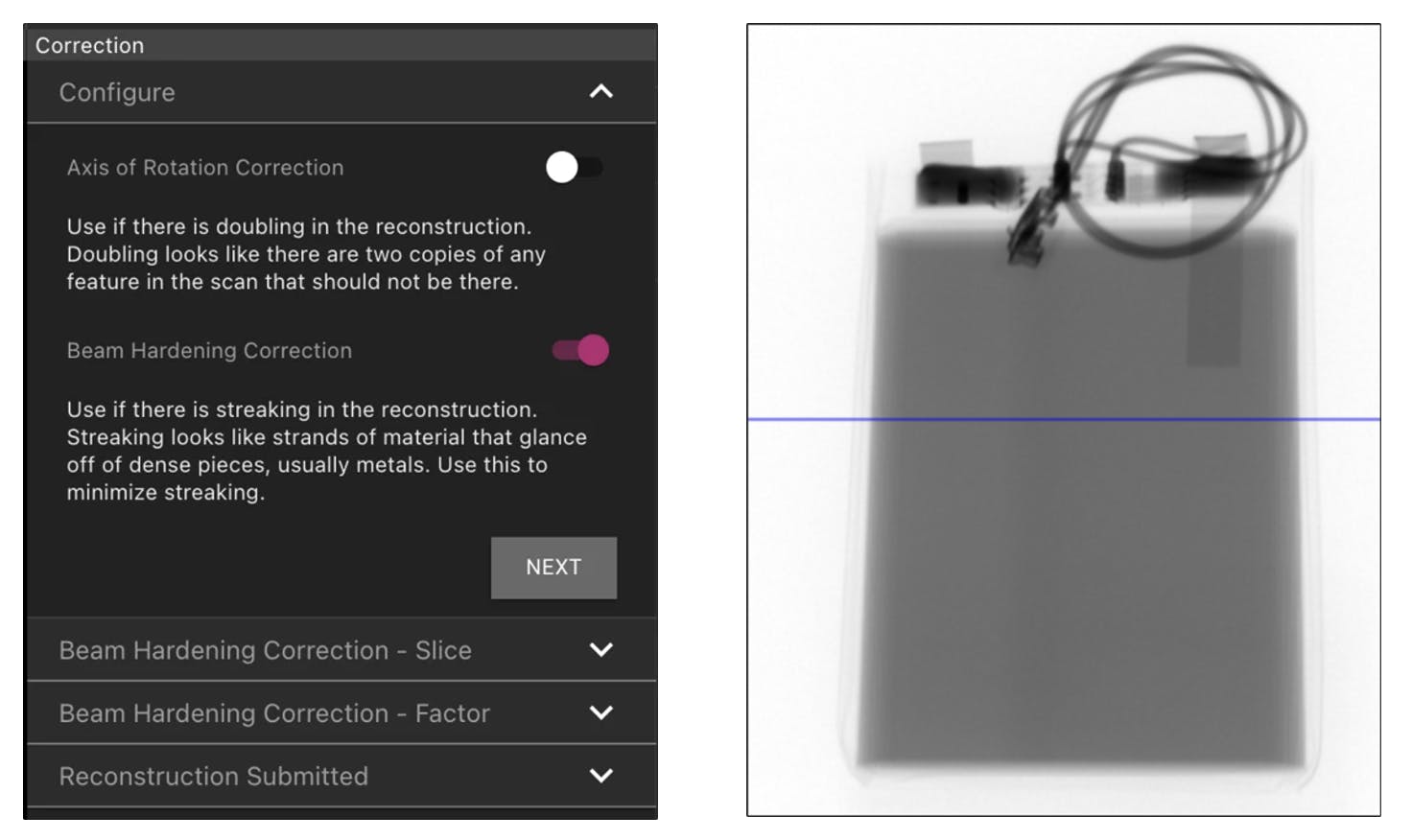
Source: Lumafield
This prompts the user with a slider on top of the scan. The point where the line intersects the part in an area of interest is shown as a darker, more dense region where beam-hardening artifacts are more likely to be present.
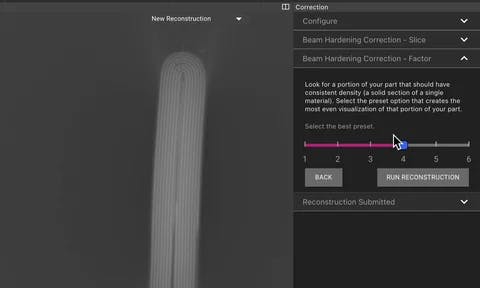
Source: Lumafield
Battery Analysis Module
In September 2024, Lumafield launched a battery analysis module in Voyager designed specifically for battery manufacturers. It simplifies and automates the inspection of battery cells, covering cylindrical, pouch, and prismatic formats, as well as different chemistries. With Ultra-Fast CT, the system can perform a scan in 0.1 seconds.
The module also provides tools to measure features like anode-cathode overhang, can circularity, and wall thickness, and detect issues such as debris, contaminants, and defects in the current collector. These capabilities are integrated into Voyager's browser interface, enabling adoption across all stages of battery development and manufacturing. The tool also works with Voyager Studies to aggregate results for trend analysis and integrates with Uplink, allowing it to process data from non-Lumafield industrial CT scanners.
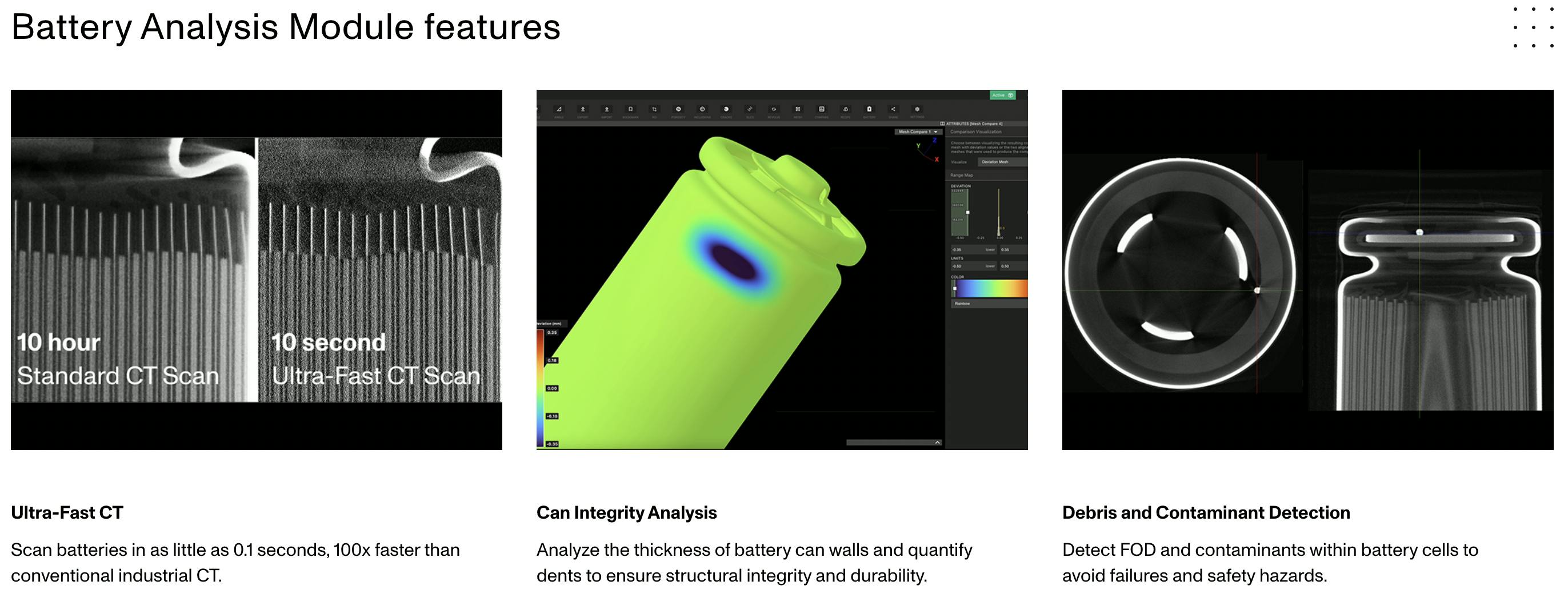
Source: Lumafield
Lumafield's Voyager software also offers a solution for automating and streamlining quality assurance processes. By utilizing what the company calls "software-defined inspection," customers can perform a single CT scan to capture comprehensive data. With that scan, Voyager allows users to conduct in-depth analysis across all relevant information at scale, effectively replacing multiple steps in traditional QA workflows. This eliminates the need for repeated inspections, enabling manufacturers to ask a range of questions and gather insights from a single dataset, making the process efficient and versatile across various operations. As Torrealba described the offering in a September 2024 interview with Contrary Research:
“If you’re scanning every single thing that you make in a factory and you run into a quality assurance problem, [but] you didn’t expect that exact thing (the original match), you can actually just create that analysis recipe, [and] run that on your entire data set. Then you can chart that statistically and say that the problem only showed up in this range of time. You scan them once and you can apply every single kind of measurement that you want.”
Atlas
Atlas is an AI agent embedded into Voyager. It is trained on engineering knowledge to identify issues like anomalies and generate annotated bookmarks that highlight features. Lumafield claims to reduce weeks of quality assurance processes to mere minutes, enabling a single engineer to accomplish what once required a dedicated team. Atlas pops up as a simple chat interface from the bottom left of the screen and is prompt-based. It can initiate workflows such as porosity analysis, CAD comparisons, and scan-to-scan comparisons.
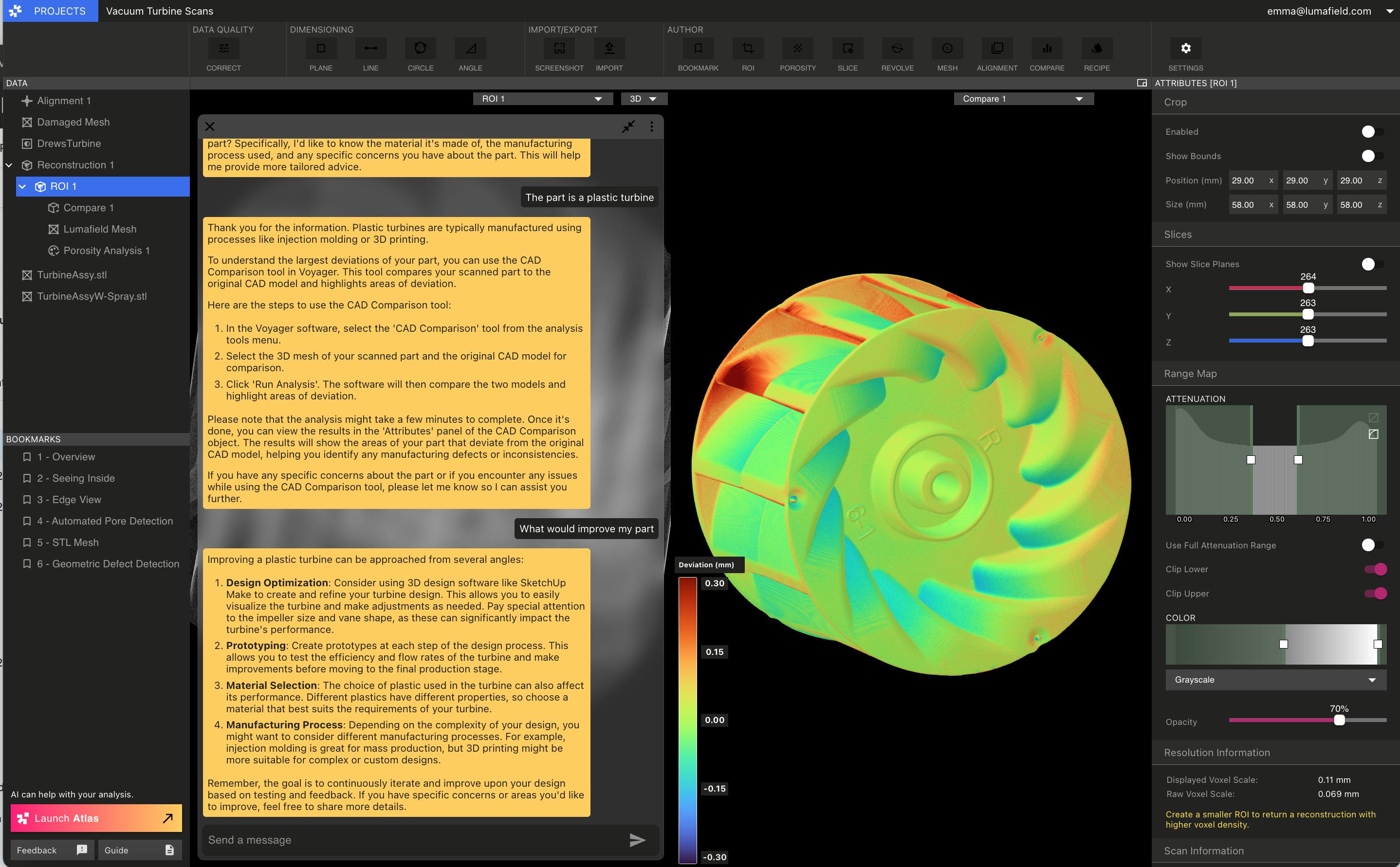
Source: Lumafield
In addition to these workflows, Atlas offers a versatile range of other tools to help analyze and understand parts better. These tools include measuring features, creating cross-sections, and visualizing data in different ways. Some of the extra features it provides are material selection insights and manufacturing process choices. For material selection, Voyager provides insights into the properties of different materials based on data from CT and surface scans. Regarding manufacturing processes, it analyzes part data and suggests the most suitable manufacturing method based on factors such as part complexity, material used, and desired finish.
Atlas also helps identify requirements for manufacturing, including applicable regulations, tolerances, surface finish, and other specifications needed for successful production. It offers analysis suggestions, such as recommending a porosity analysis for parts with complex internal structures. Additionally, Atlas aids in root cause analysis by comparing scans over time to identify defects or issues in parts. Torrealba stated in an interview for Contrary Research that the long-term vision for Atlas is:
“[To] have this system that has seen a lot of manufactured objects. You could put all of your company’s data into Atlas. All of your experience in that brain of running into a problem bringing up a new product. How do we build the corpus in manufacturing knowledge for your organization that allows you to have the best manufacturing engineer in the world on staff at all times. That’s the vision of what Atlas will become.”
Neptune
As of October 2024, Neptune was one of Lumafield’s two hardware offerings. The machine measures six feet wide by six feet tall and is under three feet deep, which means that it can fit through a standard doorway. It comes equipped with leveling caster wheels to help position it during movement without hassle. Neptune fits into any office environment, plugging into a normal 120V wall outlet, and comes out of the box with ethernet and wifi connectivity. In an interview with Contrary Research Torrealba described the hardware to be:
“...the kind of thing you would put into a quality lab in a factory. It’s going to live next to equipment from big scientific instrument manufacturing quality assurance companies that sell massive numbers of their units because they provide vital information to their customers. They do billions of dollars in revenue off of those product lines.”
Source: Lumafield
The sliding door acts as an entry point for the scanning platform. The object to be scanned is placed on this platform that sits in the middle of the open space. The platform can be adjusted horizontally and vertically when setting up a scan.
Source: Lumafield
Moving the object closer to the X-ray source will increase the magnification of the scan, whereas moving it further away will do the opposite, or decrease the magnification.
Source: Lumafield
The platform rotates 360 degrees to capture 2D X-ray images from a variety of angles. This is similar to the type of X-rays seen in medical scans. Once the object is placed in the center the user can preview what the scan may look like via the touch screen on the outside of the scanner. The user can then decide to zoom in or out and this will reflect on the preview in real time. If a user does not want to do the setup themselves, there is an auto-scan functionality, which allows the Neptune scanner to figure out the most optimal parameters for the scan.
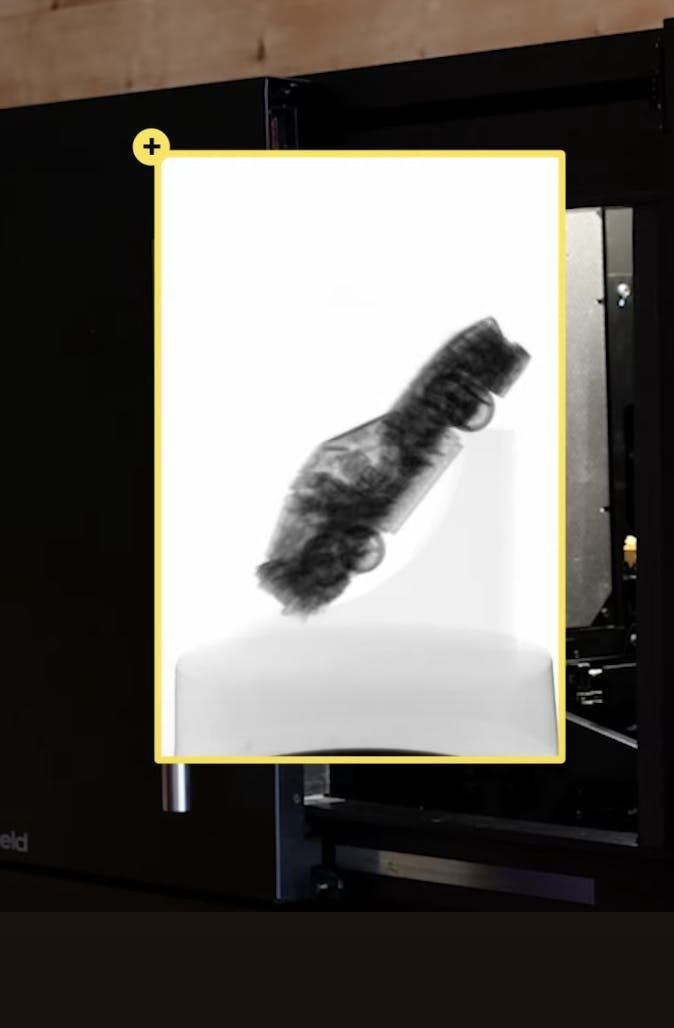
Source: Lumafield
For advanced users, there is the ability to set beam energy, current, gain, and exposure time. One of the most important features that a user can control is scan time, which directly correlates to the quality of the scan. A faster scan will take shorter X-ray exposures, which results in a noisier scan, while a slower scan will take more images and result in a sharper scan. Different materials will require different times to get a flushed-out scan. If the product is a lightweight plastic part, the scan time could be quicker, whereas a steel part might warrant an overnight scan time.
As the scan progresses, the scanner uploads continuously to Voyager, Lumafield’s software companion, which reconstructs it into a 3D model. In a single CT-scanning operation, anywhere from a few hundred to a couple thousand individual X-ray radiographs can be taken.
As of October 2024, the Neptune model came in three different configurations:
The Neptune scanner leverages AI to automate and optimize the scanning process. The system’s software uses AI models trained to adjust scan settings, such as the X-ray source, detector, and scan time, ensuring high-quality scans without requiring deep technical knowledge from the user. By answering a few questions on the touchscreen interface, users can allow the AI to handle complex multivariable optimization, similar to how one would operate a microwave. For users who want more control, Neptune also offers manual settings, enabling advanced users to fine-tune the system themselves. This balance between automation and flexibility makes Neptune accessible to both beginners and experts in the field.
Triton
Triton is a production-scale CT inspection system suitable for in-line or line-adjacent applications at high volume. It maintains a similar physical presence, with the addition of automated part handling that can integrate with factory automation systems and move parts into and out of the scanner for full lights-out operation. It also requires one standard wall outlet to power the machine.
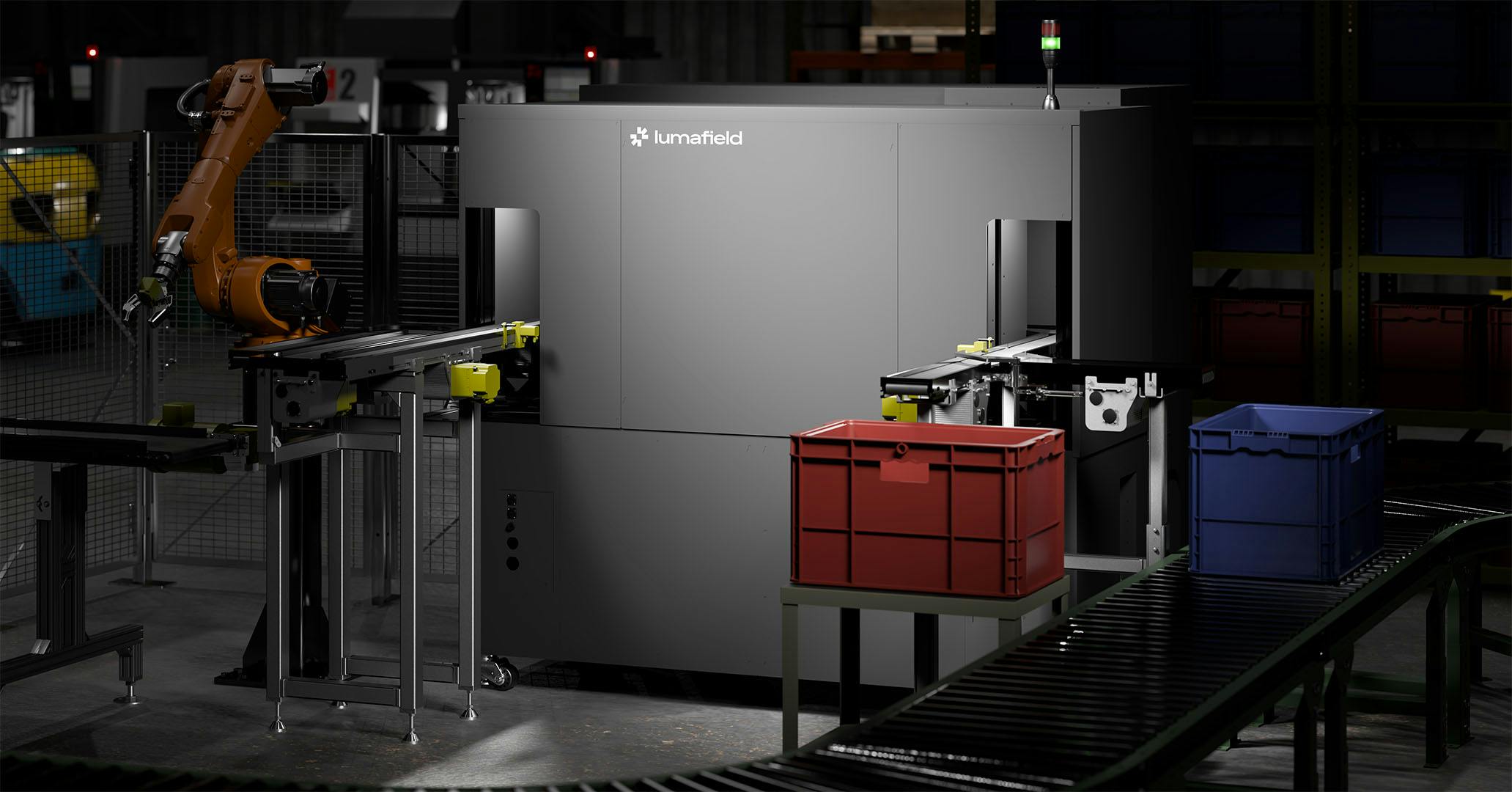
Source: Lumafield
Lumafield Neptune scanners are built to be used in both lab settings and near production lines to identify problems and develop solutions. These scanners provide detailed insights into internal structures, helping to enhance product design and ensure quality. Triton builds on this capability, enabling users to scale solutions developed on Neptunes directly into production using Lumafield’s Voyager platform.
Triton enhances manufacturing processes by enabling faster scans with automated decision-making, embedding quality assurance directly into the production line. Operating autonomously, Triton reduces human involvement, freeing engineers and other employees to focus on developing new products. Its lights-out operation eliminates labor costs and increases throughput by up to four times, according to the company, compared to manually operated Neptunes. Triton is enabled by Lumafield’s groundbreaking Ultra-Fast CT technology, which can capture CT scans in as little as 0.1 seconds. Including part movements, Triton can achieve cycle times as fast as 5 seconds, complemented by real-time intelligent analysis.
Utilizing AI and custom recipes, Triton identifies out-of-spec parts and can make go/no-go decisions. It generates data for trend spotting and process improvement, integrating with factory automation systems. For example, in packaging lines, Triton conducts batch thickness and dimensional checks to ensure quality. In automotive assemblies, it validates component alignment and electrical connections within seconds. During battery production, Triton measures anode overhang distances to optimize performance and reduce recall risks. For consumer packaged goods (CPG), it performs inspections to detect internal porosity and cracks.
Market
Customer
In a June 2024 interview, Torrealba stated that 80% to 90% of Lumafield’s customers are companies that have never had a CT scanner before. As Jon Bruner (Lumafield’s head of marketing) told Contrary Research, these are typically companies that manufacture less-expensive products at high volumes in industries where legacy CT has been cost-prohibitive, such as plastic packaging, athletic equipment, and automotive.
Companies that do have access to CT scanners might not have them on hand, but instead will need to mail the parts to a central scanning bureau to get them scanned. Lumafield helps such customers cut down on the inspection times involved in such processes. “It’s the difference between having your engineering problem answered in two hours and waiting a week” stated Bruner.
Lumafield serves use cases in a variety of different industries including aerospace & defense, automotive, athletic equipment, CPG, medical devices, batteries, and electronics. As of October 2024, some of Lumafield’s notable customers included companies like L’Oréal Group, WHOOP, New Balance, PUMA, Axon, Skydio, Milwaukee, and SharkNinja.
Lumafield’s approach to product development has been tied to the needs of its customers since its inception. While still in stealth mode, the company had paying customers who provided feedback on the quality of scans, helping fine-tune its Neptune scanner. This customer-driven development process meant that Lumafield wouldn’t build features unless they had already been validated by paying customers. By engaging with early users, Lumafield ensured that every new feature addressed real-world needs, which reduced the risk of developing unnecessary tools.
Additionally, Lumafield’s product strategy follows the 80/20 principle, focusing on building 20% of features that solve 80% of user problems. This is intended to ensure that the core functionalities of Lumafield Neptune are robust and widely applicable without over-complicating the software with features that only serve niche cases. This targeted approach is designed to allow the company to remain responsive to customer feedback and achieve efficiency in its resource allocation while serving a range of industries with diverse needs.
Market Size
The market for smart manufacturing was valued at $107.2 billion as of November 2023 and is expected to reach a market size of $611.5 billion by 2032 with a CAGR of 19.1%.
Lumafield has been able to serve use cases in a variety of multi-billion dollar industries including the US aerospace & defense industry ($496.6 billion in 2024), the automotive industry ($3.6 trillion in 2023), the athletic equipment industry ($332.6 billion in 2022), the consumer packaged goods industry ($2.1 trillion in 2022), the medical device industry ($536.1 billion in 2023), and batteries & electronics ($84.3 billion in 2024).
Competition
Nikon Metrology: Nikon is a public company founded in 1917, and has a market cap of $4 billion as of October 2024. Nikon Metrology is a subsidiary founded in 1998, expanded in 2009, and offers solutions intended for manufacturing including optical inspection and mechanical 3D imaging, similar to Lumafield. It offers four models compared to Lumafield’s two (Neptune and Triton) as of October 2024. Each of Nikon’s models is very specific to CT scanners, while Lumafield is more general. The source energies of the VOXLS 30 Series are higher than Neptune’s. It has configurations at 225kV, 320kV, or 450kV while Neptune is at 120kV, 130kV, and 190kV. Nikon’s models are larger compared to Lumafield’s and thereby can scan larger items. However, it does not offer cloud-based analysis software like Lumafield.
ZEISS: Carl Zeiss Meditec AG is a public German company with a market cap of $6.3 billion as of October 2024. Founded in 1846, ZEISS offers solutions for industrial metrology with limited optionality, including CAD comparison, dimensional measurements, thickness inspection, and tolerance or geometric dimensioning, which are also offered by Lumafield. ZEISS's options are supposedly more flexible in size and come with what is reportedly a more powerful analysis. However, the EasyTom S system, comparable to Lumafield's Neptune, supposedly has less efficiency and is less suitable for automation. The EasyTom L, which competes with the Triton, has a higher microfocus but is not designed for production line handling. Additionally, ZEISS offers the EasyTom XL, which offers a larger space to scan, but its max microfocus is lower than Neptune’s at 160kV compared to 190kV.
North Star Imaging: North Star Imaging specializes in digital radiography and CT X-ray systems. Founded in 1986, it was a private company that was acquired by a public company, Illinois Tool Works, in 2010. Illinois Tool Works has a market cap of $75.9 billion as of October 2024. North Star Imaging offers 12 models of physical scanners compared to Lumafield's two. Application download for individual types of analysis is a Windows-based software package, which must be downloaded to a laptop and is not accessible online, unlike Lumafield, which works on any laptop and is a more holistic offering with a broader set of features enabled from the start. Lumafield also supports the upload of user scans, provided they fit the supported format. A unique feature of North Star Imaging is its 4D scanning, which allows users to observe wear and tear over time.
Waygate Technologies: Founded in 2004, Waygate Technologies, formerly known as GE Inspection Technologies is a subsidiary of Baker Hughes as of 2017. Baker Hughes is a public company with a market cap of $37.5 billion as of October 2024. It offers a broader range of sizes, CT systems, and inline inspection solutions.
Comet Yxlon: Comet Yxlon is a subsidiary of Comet Holdings and was founded in 1998. Comet Holding is a public company with a market cap of $2.8 billion as of October 2024. Like other competitors, it offers multiple high-powered CT scanners (up to 600kV), and each model has a specific focus. It also has software packages for a variety of different purposes.
Business Model
Voyager
Source: Lumafield
Lumafield’s Voyager cloud-based analysis software is included with every Neptune scanner. According to information Lumafield shared with Contrary Research, standard Voyager configuration includes ten editor seats and unlimited viewer seats to maximize Voyager’s power as a collaborative platform for engineers.
Lumafield also shared with Contrary Research that Voyager is available independently of the Neptune and Triton scanners, allowing companies that already own a legacy CT scanner to visualize and analyze their data collaboratively through the cloud. This option is called Voyager Uplink.
Neptune & Triton
Source: Lumafield
As of October 2024, there was no public pricing information available for the Triton, as it is priced on a per-company basis. However, for Neptune, Lumafield has two pricing levels:
Standard: The standard package starts at $75K. It includes onsite hardware, unlimited scanning and storage with three editor seats, unlimited viewers, service and support from the team, core Voyager features plus comparative tools, 3D viewing and slicing, 2D measurements, acquisition modules, faster scanning, high resolution, and expanded scan volume.
Production: The Production package has custom pricing. It includes all features of the Standard package along with automated operation with loading and unloading parts for high throughput, a production dashboard, and recipe execution.
Traction
As of March 2023, one year after Lumafield came out of stealth, Torrealba stated that the company shipped more than ten but fewer than 100 machines, without further indication as to the exact number. In 2022, it was reported that Lumafield had quietly built a customer base of “dozens” of companies. As Torrealba told Contrary Research in a September 2024 interview:
“...by [the summer of 2022], we were doing seven figures of ARR and we’ve tripled every year since then. We’re past eight figures of ARR by this point. This is a company that’s growing at the speed of an enterprise SaaS company. We make margins that are best in class, and we close deals really quickly.“
As of October 2024, these customers range from technology startups to publicly traded enterprises. In September 2024, Torrealba stated that the company was “achieving 70%+ gross margin right now with the way [it’s] operating the business” and that “there’s also things on software [Lumafield] can do to increase margins.”
Valuation
As of October 2024, Lumafield had raised a total of $67.5 million from investors including Lux Capital, Kleiner Perkins, Data Collective, and Build Collective. In September 2022, Lumafield raised a $35 million Series B round led by Spark Capital. In June 2024, Lumafield reportedly raised an undisclosed amount of additional Series B funding from Shane Neman. Prior rounds include a seed round led by Lux Capital and Kleiner Perkins in August 2019, who also invested in a $32.5 million Series A round led by DCVC in January 2020.
Lumafield’s comparable public companies, like Nikon or Illinois Tool Works, are broader conglomerates with subsidiaries involved in optical inspection. For example, ZEISS “is a multinational medical technology company [manufacturing] tools for eye examinations and medical lasers as well as solutions for neurosurgery, dentistry, gynecology and oncology.” As a result, it’s less clear what Lumafield could potentially trade at as a public company. The lack of standalone public companies with its focus could also indicate that Lumafield may end up getting acquired by a larger conglomerate.
Key Opportunities
Leveraging AI & Data
As of November 2023, the cost for AI and LLMs began to decrease. Atlas, Lumafield’s AI software companion, is an early indication of that capability, but building it into the inline process can further improve the quality of each product reviewed. Further leveraging AI can better inform a user’s understanding of wear and tear on the products, which can deepen the understanding of future models, acting as a two-way solution.
AI could also be leveraged to create a more aware AI tool similar to Ramp Tour, an AI agent from Ramp, prompting the user to conduct new things that it might not have known could be done, without explicit instruction as a means of driving engagement on the piece being scanned. Better information, or knowledge, will improve results which improves bottom-line ROI and builds a natural flywheel for Lumafield engagement.
Manufacturing Optimization
Lumafield has solutions and services that work in line with manufacturing. Torrealba references a conversation with a friend about how 90% of individuals under 30 do not make it past the 90-day probationary period doing factory labor.
As a result, manufacturing has to deal with a shrinking workforce, all while output requirements continue to rise. This also presents an opportunity to bring manufacturing closer to a ‘lights-off’ approach by expanding its product line to encompass attachments that can be retrofitted to its scanners and reduce the requirement for labor needs on the manufacturing line. Lumafield could play a key role in automating the quality control processes within these more automated facilities in the future.
Expanding To Enterprise
Lumafield considers itself positioned as a generalist low-cost solution for CT scanners in the industry. However, the company has partnerships with large conglomerates and has shown substantial ROI for these companies, allowing them to stay competitive. For example, Lumafield reduced the time to decision from three weeks to three days for a conglomerate.
While Lumafield has established partnerships in racing and automotive parts, there is also potential to address larger enterprise opportunities in aerospace or automotive. For example, in 2023 the budget cap for R&D was $135 million per car as cars are continuously undergoing even the slightest tweaks to make sure they are performant and flawless. Using AI and modeling to suggest new improvements could save significant dollars on those engineering processes.
Fully Autonomous Manufacturing
Lumafield’s long-term vision extends beyond CT scanners, aiming to change manufacturing by integrating robotics, AI, and automated systems into a workflow. It envisions a future where humans are removed from many of the processes, with robots and AI handling production and inspection tasks without the need for human intervention. This vision is built on a foundation of creating products that deliver immediate value to customers, serving as building blocks toward fully automated manufacturing systems.
Lumafield aims to develop a system where every input in manufacturing, from materials and temperature settings to pressures and flow rates, is captured, analyzed, and optimized by its technology. Once a part is created, it would pass through a Lumafield scanner for inspection, feeding data back into the company's software to continuously fine-tune the production process. Over time, this system would enable companies to identify and correct deviations in quality by referencing the vast amount of scan data Lumafield has accumulated, effectively automating quality control at every stage of manufacturing, eliminating repetitive tasks and helping maximize efficiency.
Eventually, Lumafield hopes to create a fully integrated manufacturing ecosystem. By scanning everything a company produces and tracking all production parameters, Lumafield can offer preemptive design and manufacturing insights. This would allow manufacturers to optimize their processes in real time, making it possible to predict and correct quality issues before they occur. It’s a vision of a fully autonomous manufacturing process where AI and data-driven insights optimize every step of production, from design to final inspection.
Key Risks
Competition
Given the diverse segments and industries that Lumafield’s industrial CT scanners can address, the company faces competition from established players like Nikon or ZEISS. While Lumafield has mentioned that it has a few large clients, as Lumafield expands further into the aerospace or medical industries, it may encounter many competitors with decades of experience. However, Lumafield could demonstrate substantial value to effectively replace legacy tools either by expanding the product line to fit larger items or by continuing to innovate on existing processes.
High R&D Costs
Rapid technological advancements in the field of industrial CT scanning could outpace Lumafield's offerings. Developing high-end features like sub-micron resolution, AI integration, and advanced software requires substantial investment in R&D. Competitors with more resources may develop superior technology, making it challenging for Lumafield to keep up without substantial investment in R&D.
Balancing the need to invest in R&D with the need to maintain affordable pricing for products can be challenging. High R&D costs can drive up the price of Lumafield’s scanners, potentially reducing its competitive edge in the market. A larger competitor of Lumafield can also leverage an extensive R&D facility and partnerships with research institutions to accelerate innovation cycles.
Summary
Lumafield was founded to modernize quality control in manufacturing by replacing outdated tools like bandsaws and calipers and traditional destructive testing methods with advanced CT scanners. The company aims to solve long-standing issues in quality assurance by making CT scanning technology more affordable and its accompanying software more accessible to a wide range of industries. Lumafield’s technology serves diverse sectors such as aerospace and CPG, offering flexibility across different use cases. While its pricing gives it a competitive edge, the high costs associated with research and development remain a challenge. Moving forward, Lumafield has the opportunity to solidify its position by expanding its product offerings and continuing to integrate AI-driven solutions to meet the evolving needs of its customers.